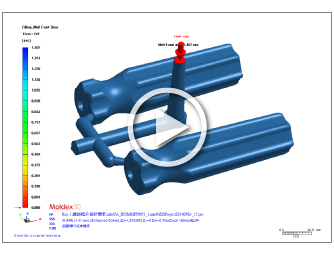 |
|
First Prize in Americas Region: Stanley Black & Decker
Predicting Tooling Problems before Production
Industry: Machinery & Equipment
Team Members: Bob Scillia, William Lai, Frank Tsai
Company/Team Introduction:
Stanley Black & Decker is a world-leading provider of tools and storage, commercial electronic security and engineered fastening systems, with unique growth platforms and a track record of sustained profitable growth.
|
Story Overview/Challenge:
William Lai is a DTV team leader at Stanley Black & Decker. His team conducted three projects with the help of Moldex3D to simulate and solve the potential tooling or structural issues. First, it was hard to know accurately where the weld line would form. From their historical testing, the part would crack near the screw boss if a weld line exists. Second, the use of bi-material (ABS and TPE) for improved comfort, grip, and visual appeal of their hand tool was difficult to achieve good bonding without testing in actual mold. Following the vendor’s experience and suggestions sometimes still could not resolve the issue which resulted in the need of costly tool fixing and delayed project schedules. Third, it was not easy to produce a screwdriver handle grip using a translucent material with a very thick cross section. They faced the issues of both cold weld lines and misty surface appearance.
Solution:
For the first case, Moldex3D could accurately predict the weld line position. Therefore, the team could know how to modify the inner structure to change the weld line position to attain the structural strength they needed in drop test without having costly design changes during tooling phase. For the second case, Moldex3D could predict the ABS and TPE bonding temperature and molding conditions. Thus, it helped them optimize the molding conditions to achieve the best bonding before the tooling started. For the third case, Moldex3D could simulate multiple injection conditions using different gate designs in order to obtain the gate shape and dimension that could eliminate the cold weld line and misty surface appearance issues. They were eliminated as the plastic flowed very smoothly after the injection point was relocated. In addition, the core shift value of the screwdriver metal could be accurately obtained, preventing the tooling issues.
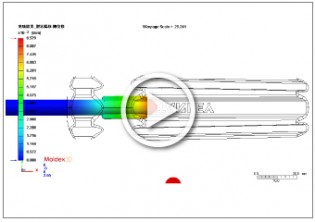
Results/Benefits:
- Changed weld line position to pass the drop test
- Optimized molding conditions to have best ABS and TPE bonding
- Eliminated cold weld lines or misty surface appearance
- Accurate core shift value for screwdriver handle grip case
- Reduced tooling time and cost
Product Used:
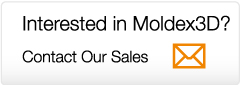
|