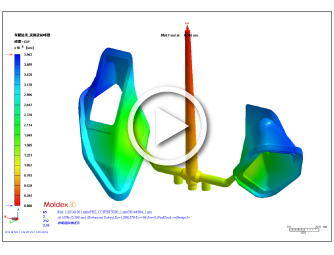 |
|
Special Prize in Greater China Region: GIZMO Plastics Tech. Co., Ltd.
Moldex3D Simulation Helps Reduce Warpage in an Outboard Fuel Filter Part
Industry: Mold & Die
Team Leader: Feng-Yi Yen
Team Leader: Yi-Da Huang, Ming-Hsien Hung, Shih-Wei Tseng
Company/Team Introduction:
Gizmo Plastics Technology is a leading plastic injection molding OEM (Original Equipment Manufacturer) and second-tier supplier for many worldwide automotive and transportation brands, including KYMCO, YAMAHA, with more than 30 years experience.
|
Story Overview/Challenge:
Flatness for outboard fuel filter components is critical to preventing fuel/air leaks. In this case, the injection molded fuel filter, which consists of an upper and a lower cover, failed to pass the leak test due to excessive warpage. Gizmo’s design team must understand and identify the root cause of warpage, so the product can pass the leak test and get back into production in short order.
Solution:
With Moldex3D, GIZMO quickly identified the two main factors which led to warpage are non-uniform cooling and fiber orientation. GIZMO also used Moldex3D to evaluate the feasibility of proposed design changes. The warpage simulation analysis showed that adding baffles would help improve the temperature difference between the core and cavity mold surfaces. Additionally, Moldex3D simulation results assisted Gizmo in determining the best gate location that could contribute better fiber orientation to reduce warpage.
Results/Benefits:
- Achieved higher weld quality
- Improved warpage by 40%
- Reduced mold trials and rework
Product Used:
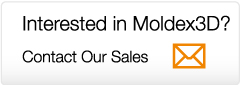
|