ผู้นำด้านซัพพลายเออร์ชิ้นส่วนยานยนต์ระดับโลก ใช้
ประโยชน์จากการวิเคราะห์ด้วย
Moldex3D เพื่อการสร้างความมั่นใจในด้านการ
ออกแบบชิ้นงาน
![]() |
|
ด้วยความที่มีสาขาถึง 320 แห่ง, รวมทั้งมีศูนย์วิจัยและพัฒนา 30 แห่ง ใน 34 ประเทศทั่วโลก, Faurecia ในขณะนี้เป็นผู้นำระดับโลกในธุรกิจ 4 ด้าน ได้แก่ ที่นั่งรถยนต์, ระบบภายในและนอกรถยนต์,และเทคโนโลยีควบคุมการปล่อยก๊าซ นอกจากนี้ทางบริษัท Faurecia ยังเป็นผู้นำอันดับ 1 ด้านโครงที่นั่งและระบบกลไก , เทคโนโลยีควบคุมการปล่อยก๊าซ และงานภายในรถยนต์ และยังเป็นซัพพลายเออร์อันดับ 3 ในด้านระบบที่นั่งทั้งระบบ และมีชื่อเสียงอันดับต้น ๆ ของยุโรปในด้ายงานภายนอกยานยนต์ Faurecia ทีศูนย์วิจัยและพัฒนา 1แห่งและมีโรงผลิต 2 ที่ในเมือง Pune (ที่มา: www.faurecia.com )
สรุป
ด้าน ในกรณีนี้ได้แสดงให้เห็นถึงความสำคัญด้านรูปลักษณ์ของชิ้นส่วนภายในรถยนต์ : แผงคอนโซล fascia เนื่องจากส่วนนี้เป็นบริเวณที่มองเห็นได้ง่าย และมีระดับคุณภาพความงามและรูปลักษณ์ที่เป็นที่ต้องการ รอยตำหนิที่มองเห็นได้ เช่น รอยยุบ (sink marks), weld lines และ รอยการไหล (flow marks) ควรได้รับการควบคุมให้เห็นน้อยที่สุดบนชิ้นงาน และควรลดการเกิด warpage เพื่อรักษาขนาดชิ้นงานให้มีความแม่นยำให้อยู่ในเกณฑ์ที่ยอมรับได้ เพื่อสร้างความมั่นใจในการนำไปประกอบชิ้นส่วนต่อไป อย่างไรก็ตามปัญหาเหล่านี้ค่อนข้างท้าทายที่จะควบคุมการเกิด warpage และกำจัดรอยตำหนิโดยอาศัยความรู้และประสบการณืด้านแม่พิมพ์ ดังนั้นทาง Faureciaจึงนำ Moldex3D มาใช้ในการจำลองซิมมูเลชั่นเพื่อช่วยในการตัดสินใจและสร้างความมั่นใจในการออกแบบชิ้นงานแลแม่พิมพ์ที่เหมาะสม ซึ่งการวิเคราะห์ด้วย Moldex3D ทำให้สามารถเห็นแถบสีของสัดส่วนแม่พิมพ์ รวมไปถึงการวิเคราะห์รายละเอียดในขั้นตอน filling, packing, cooling และ warpage และยังช่วยทบทวนวิธีการแก้ปัญหารอยตำหนิที่เป็นไปได้บนชิ้นงาน อีกทั้งแก้ปัญหาการผลิตที่ยุ่งยาก ยิ่งไปกว่านั้น Faurecia สามารถไปถึงเป้าหมายและประสบความสำเร็จในการแก้ปัญหารอยตำหนิได้อย่างงดงาม
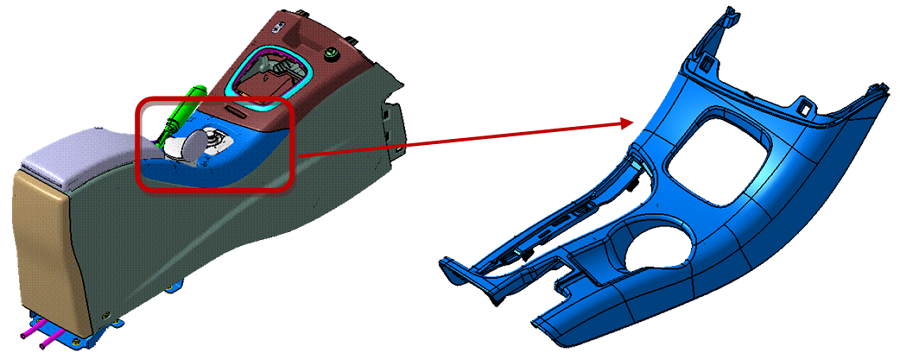
รูปที่ 1: ในกรณีนี้แสดงให้เห็นถึงความสำคัญของชิ้นส่วนยานยนต์ : แผลคอนโซล fascia
ความท้าทาย
- หลีกเลี่ยงรอยตำหนิที่มองเห็นได้บนชิ้นงาน เช่น รอยยุบ (sink marks), weld lines และ รอยการไหล (flow marks)
- ลดการเกิด warpage เพื่อรักษาขนาดชิ้นงานให้มีความแม่นยำให้อยู่ในเกณฑ์ที่ยอมรับได้เมื่อนำชิ้นงานไปประกอบกับชิ้นส่วนอื่น
- ควบคุมอุณหภูมิและความดันให้เหมาะสม เพื่อหลีกเลี่ยงการเกิด over-packing และ short filling
วิธีการ
เป้าหมายของโครงการนี้คือการเอาชนะอุปสรรคและความท้าทายระหว่างระยะออกแบบและพัฒนาแทนที่จะใช้เครื่องมือและทดลอง แม่พิมพ์ในภายหลัง ในกรณีนี้ Moldex3D eDesign analyses ซึ่งประกอบด้วย filling, packing, cooling และ warpage จะถูกนำไปใช้ประโยชน์ในการศึกษาและออกแบบที่เหมาะสม
ประโยชน์
- สามารถหลีกเลี่ยงการเกิด weld lines ในบริเวณที่มองเห็นง่าย
- ลดการโก่งตัวของชิ้นงานให้อยู่ในเกณฑ์ที่ยอมรับได้เมื่อนำชิ้นงานไปประกอบกับชิ้นส่วนอื่น
- ลดค่าใช้จ่ายในการปรับแต่งลง 68%
- ลดอัตราการเกิดscrap ให้น้อยลงที่สุด
กรณีศึกษา
ในกรณีนี้, Faurecia ได้นำเอา Moldex3D’s eDesign full package มาใช้ในการวิเคราะห์เชิงลึกกับสิ่งที่อาจจะเกิดขึ้นในแม่พิมพ์จริงแบบดั้งเดิม จากผลการจำลองซิมมูเลชั่นของ Moldex3D ทำให้ทางบริษัท Faurecia พบว่าแบบดั้งเดิมจะมีปัญหาการเกิด weld lines บนชิ้นงานและมีความรุนแรงพอที่จะเกิด warpage ซึ่งเป็นการเสียรูปชิ้นงานแบบบิดเบี้ยว และอาจจะเป็นสาเหตุให้ประกอบชิ้นงานล้มเหลวในภายหลัง เนื่องจากความดันที่รุนแรงและอุณหภูมิที่ลดลง และเกิดการ over-packing ซึ่งจะพบที่บริเวณเกท ส่วน การเติมเนื้อพลาสติกเหลวเข้าไปน้อย (short filling) มักจะพบบริเวณที่เป็นสัน เพื่อเป็นการแก้ปัญหาข้างต้นและผลิตชิ้นงานให้ออกมามีรูปลักษณ์ที่สวยงาม ทางบริษัท Faurecia จึงมีวัตถุประสงค์ที่จะใช้ระบบการป้อนแบบต่างๆ พร้อมทั้งเปลี่ยนแปลงความหนาชิ้นงานเพื่อแก้ปัญหาดังที่กล่าวมาข้างต้น
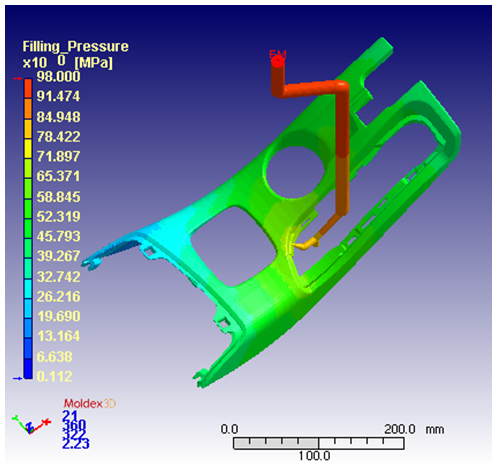
รูปที่ 2: ระบบการป้อนเนื้อพลาสติกแบบดั้งเดิม : แบบมี hot drop 1 ที่ และ inverse sub-gate1 ที่
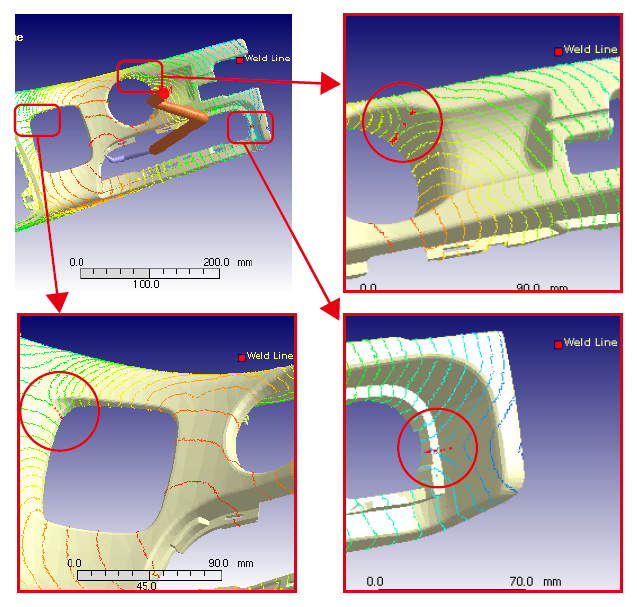
รูปที่ 3: เนื่องจากการวิเคราะห์ด้วย Moldex3D’s filling analysis พบว่า weld-lines จะปรากฏอย่างเห็นได้ชัดบนชิ้นงานแบบดั้งเดิม
ในขั้นแรก จากความจริงที่ว่าเป้าหมายหลักของโครงการนี้คือหลีกเลี่ยง/ลดปัญหารอยตำหนิ เช่น รอยยุบ (sink marks), weld lines และ รอยการไหล (flow marks) ฯลฯ ทาง Faurecia ได้แนะนำให้ลดความหนาใน fillets (ดังรูปที่ 4) ซึ่งเป็นการเลี่ยงผลที่มุมและการเกิด warpage ในทิศ Y และ Z นอกจากนี้ การเปลี่ยนแปลงความหนาชิ้นงาน ซึ่งทาง Faurecia แก้ไขระบบการ feeding ซึ่งจะช่วยควบคุมความดันดันและอุณหภูมิที่ลดได้ดีขึ้น ภายในคาวิตี้ ทาง Faurecia ได้เพิ่ม hot nozzle ในการฉีดแทนที่จะใช้เพียงแค่ nozzle อันเดียว จากนั้นได้เพิ่มกิ่ง cold runner ที่มี submarine gates เพื่อทำให้การไหลเป็นเนื้อเดียวกันมากขึ้น ส่วนส่วนที่เป็นครีบที่ได้จากการฉีด จะถูกเพิ่มเข้าไปที่ชิ้นงาน (ดังรูปที่ 5) จากผลการจำลองซิมมูเลชั่นด้วย Moldex3D แบบที่แก้ไขพิสูจน์ให้เห็นว่าสามารถปรับปรุงรอยตำหนิที่มองเห็นได้และให้ผลออกมาเป็นบวก
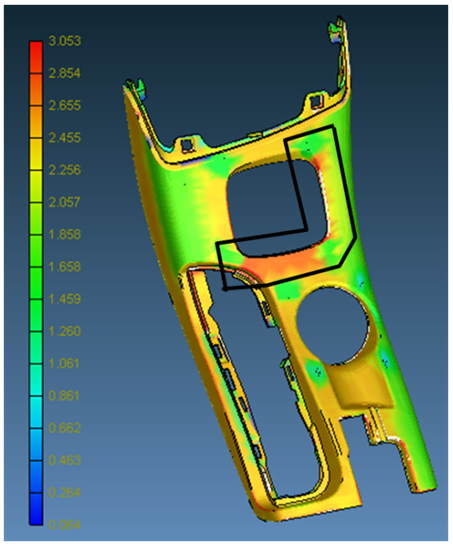
รูปที่ 4:บริเวณที่เป็นวงกลมแสดงให้เห็นการเปลี่ยนแปลงความหนาชิ้นงานในแบบที่แก้ไขแล้ว
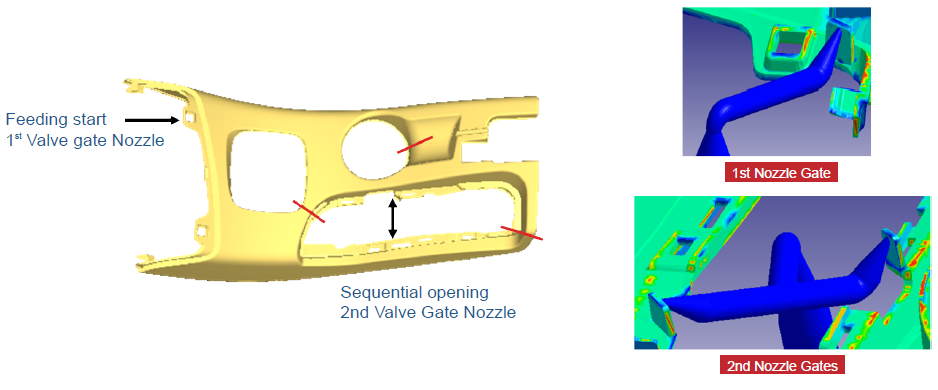
รูปที่ 5: การออกแบบแก้ไข โดยเพิ่ม hot nozzle และเพิ่มกิ่ง cold runner เข้าไปในระบบการ feeding
The following Moldex3D’s analysis results show a significant improvement in the weld line locations in the revised design. The weld lines were successfully moved to the corners, the less visible areas of the part (Figure 6).
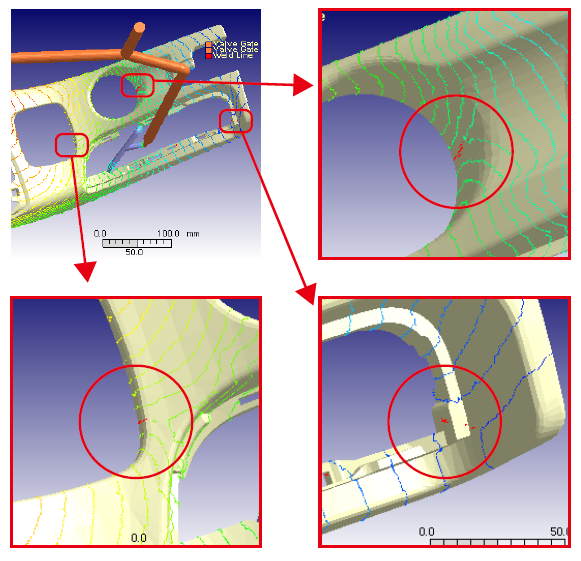
รูปที่ 6: weld lines ทั้งสองตำแหน่งจะถูกย้ายไปอยู่มุมและเหลือเพียงตำแหน่งเดียว(ขวาบน) ซึ่งมองเห็นได้ แต่ก็จะถูกบดบังเมื่อประกอบกับชิ้นงานอื่น ๆ
จากนั้นทาง Faurecia ได้ดำเนินการศึกษาความสัมพันธ์ระหว่างผลการจำลองด้วยข้อมูลซิมมูเลชั่นกับการลองฉีดขึ้นรูปชิ้นงานจริง เพื่อที่จะสำรวจว่า การจำลองซิมมูเลชั่นมีความแม่นยำมากแค่ไหนและดูว่าคำแนะนำจะทำงานอย่างไร ซึ่ง Moldex3D’s filling และการทำนายรอยตำหนิที่ได้จากการเติมสอดคล้องกับการฉีดขึ้นรูปชิ้นงานจริง (รูปที่ 7 และ 8)
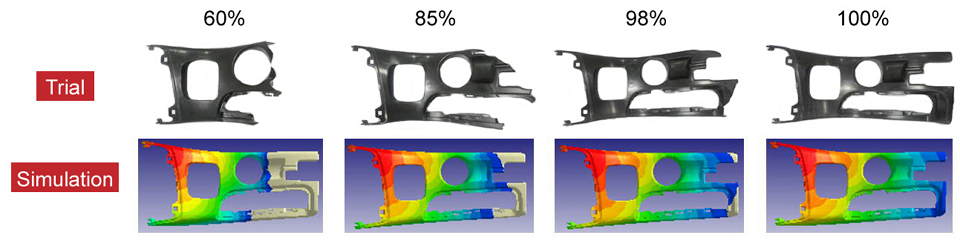
รูปที่ 7: การทำนายด้วย Moldex3D filling มีความสอดคล้องกับการทดลองฉีดขึ้นรูปชิ้นงานจริง
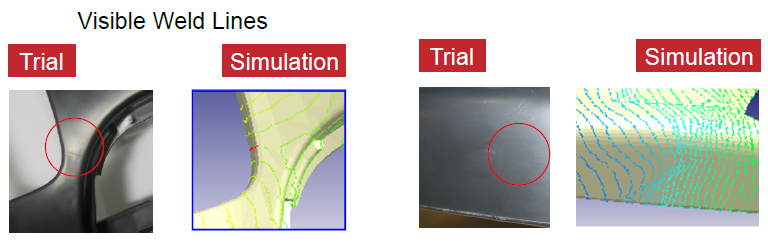
รูปที่ 8: ชิ้นงานที่ได้จากการฉีดขึ้นรูปจริงจะพบ weld line (ซ้าย) และมีการเปลี่ยนแปลงความมันเงาของชิ้นงานในบริเวณที่เกิดการไหลแบบ hesitation (ขวา)
จากการทดสอบฉีดขึ้นรูปชิ้นงานจริง การทำนาย warpage ด้วย Moldex3D ได้ถูกพิสูจน์ให้มีความสมเหตุสมผลมากขึ้น โดยแบบที่มีการแก้ไข ชิ้นงานจะโก่งตัวลดลงทั้งในทิศ Y และ Z ดังนั้น ปัญหา warpage จึงลดลงและสามารถนำไปประกอบกับชิ้นส่วนยานยนต์อื่นๆ ต่อไปได้
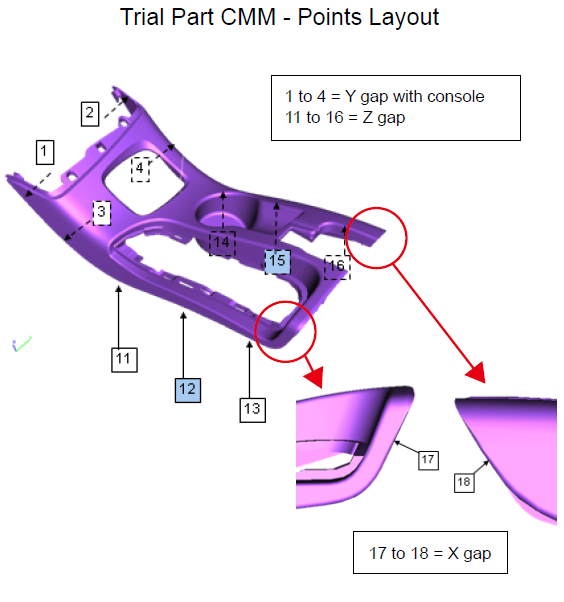
รูปที่ 9: ชิ้นส่วน CMM ที่ทำสี ซึ่งจะนำไปประกอบกับคอนโซลเพื่อตรวจว่าจะเกิดช่องว่างหรือไม่
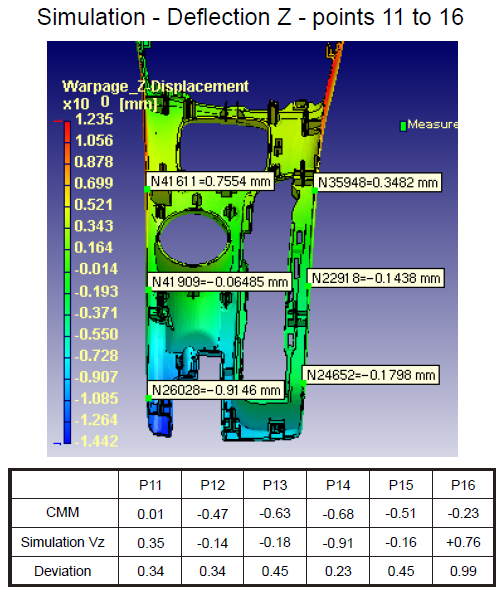
รูปที่ 10: การเปรียบเทียบ warpage ระหว่างผลจากการจำลองซิมมูเลชั่น และการสร้างชิ้นงานจริง พิสูจน์ให้เห็นว่าใกล้เคียงกับความเป็นจริงมาก
ผล
จากผลการจำลองซิมมูเลชั่นที่แม่นยำด้วย Moldex3D ทางบริษัท Faurecia สามารถใช้ข้อมูลจากการซิมมูเลชั่นไปประยุกต์ปรับค่า filling และ packing ให้เหมาะสมขึ้น และสามารถหลีกเลี่ยงการเกิด weld บนชิ้นงาน อีกทั้งชิ้นงานจะโก่งตัวลดลงทั้งในทิศ Y และ Z ทำให้ชิ้นงานมีความแม่นยำอยู่ในเกณฑ์ที่ยอมรับได้เมื่อนำชิ้นงานไปประกอบกับชิ้นส่วนคอนโซลต่อไป
นอกจากนี้ ด้วยผลการจำลองซิมมูเลชั่นด้วย Moldex3D ที่นำไปประยุกต์เข้ากับขั้นออกแบบและพัฒนา ซึ่งโดยปกติแล้วค่าใช้จ่ายในการปรับแก้แม่พิมพ์คิดเป็น 4% ของต้นทุนการผลิตทั้งหมด โดยสามารถลดลงถึง 68% มากไปกว่านั้นอัตราการเกิด scrap ลดลง การเปลี่ยนแปลการออกแบบในแต่ละแบบสามารถจำลองและวิเคราะห์ด้วย Moldex3D ดังนั้น Faurecia จึงสามารนมั่นใจที่จะตัดสินใจในทุก ๆขั้นที่มี การพัฒนาผลิตภัณฑ์ให้เหมาะสม โดยได้ชิ้นส่วนมีระบบการ feeding ที่เหมาะสม ทำให้สามารถยืดอายุการใช้งานเครื่องมือ ,อัตราการทิ้งชิ้นงานคุณภาพไม่ดีลดลง ซึ่งเป็นความสำเร็จที่สมบูรณ์แบบของโครงการนี้