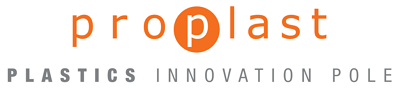
- 顧客名:Proplast
- 国:イタリア
- 業種:調査・教育
- 導入ソリューション:Moldex3D Advanced
Proplast社は、塑性加工産業に関わる調査、技術革新、人材教育に特化した企業として1998年にイタリアのアレッサンドリアで設立されました。2008年5月には、Proplast社は塑性加工関連企業向けの技術サービスセンターの敷地をそれまでの3倍となる3,500平米に拡大しました。
4名の創業メンバー(Bayer、Basell、Guala、Mossi & Ghisolf)が始めたProplast社は、塑性加工に携わるその他の企業や団体、大学などの協力を得て大きく成長しました。(出典: www.proplast.it)
本プロジェクトはProplast社主導のもと、Engel Italia社、Trexel社、Onni-stamp社の協力で行われました。
概要
本プロジェクトにおけるProplast社の目標は、MuCell® 技術導入のあらゆる段階にある顧客企業をサポートすることでした。そのサポートはパーツや金型の設計から、MuCell® 技術を用いた成形試験から金型の試作に至るまでを網羅しています。その道のりは困難かつ複雑なものでしたが、Proplast社はMuCell® 技術の支援ツールとして Moldex3D のソリューションを利用し、エンジニアたちによる全工程の確認と、パーツと金型の設計の最適化によって最終的にプロジェクトを成功に導きました。
課題
この事例の最大の課題は、MuCell®技術を正確に予測し然るべく最適化を行うことでした。
MuCell® 技術の効果を深く理解するために、次の4つの項目を設定しました:
- ひけ
- 反り変形
- セルサイズの予測と妥当性評価
- セル密度の予測と妥当性評価
プロセスの各ステップでMoldex3Dによる解析を行いました。
評価・計測・結果比較を詳細に行うためパーツ設計を細かく指定
ソリューション
Moldex3Dの解析を利用して、既存の射出成形技術とMuCell®技術による射出成形の両方の解析を行いました。ソフトウェア解析を元に各工程の結果を確認したProplast社は、既存技術とMuCell®技術の運用上の違いを理解していきました。さらに、セルの寸法・セル密度・セル分布を含むミクロセル射出成形に関してより詳しい解析を求めたProlast社の期待に、Moldex3Dが応えました。
パーツ設計
メリット
Moldex3D は、MuCell®技術利用時のあらゆる場面でシミュレーション解析を可能にしました。Moldex3Dの解析で得られた有効なデータからMuCell® への理解を深めたProplast社は、パーツ・金型の設計を最適化し、さらには同社顧客のMuCell® 技術導入にあたって積極的な提案を行いました。
Moldex3DのMuCell® 解析の構成内容:
- プロセス設定
- サイクルタイム
- 圧力
- 締め付け力
- 膨張/軽量化
- 体積の低減/ひけ
- 反り変形/残留応力分布
- 局所セルサイズ
- セル分布とセル密度
ケーススタディ
MuCell® 射出成形の解析は、 MuCell® 技術導入による真の利点を理解することでMuCell®技術の予測全般に役立ちます。Moldex3D解析はMuCell® 技術の次のような場面の理解に有用です:
1. ひけ:
圧縮成形 (左):ひけあり / MuCell® (右): ひけなし
実験的に金型を試作したところ、圧縮成形とMuCell® 技術による成形の双方でひけを精度よく予測できていたことがわかりました。また、この例は、MuCell® 技術がひけを効果的に除去できることも明らかにしました。
2. 反り変形:
圧縮成形 (左) よりもMuCell® (右)の方が反り変形が少ない
Moldex3Dの解析は、圧縮成形採用パーツとMuCell® 技術採用パーツ双方のコーナー効果を予測し、同時に、実際のパーツ成形前にMuCell® 技術による変形への効果の可視化に役立ちました。
公称寸法 | 圧縮成形 | MuCell® | 差異(%) | |||
解析結果 | 実寸法 | 解析結果 | 実寸法 | |||
A | 110 | 108,76 | 109,17 | 109,22 | 109,16 | -0.05 |
B | 200 | 198,10 | 198,64 | 198,76 | 198,72 | -0.02 |
C | 200 | 198,61 | 198,92 | 199,18 | 198,86 | -0.29 |
D | 110 | 109,21 | 109,30 | 109,52 | 109,20 | -0.29 |
解析結果およびパーツの実寸法から、MuCell®技術利用による変形の低減が確認されました。
3. セルサイズの予測と妥当性評価:
MuCell® プロセスでは、セルサイズの予測が重要です。一様なセル分布と適切なセルサイズはパーツの品質と機械的強度に深く関わるため、実際の生産前に正しい設計を導くには正確な予測が必要となります。この事例では、主に次の3か所の妥当性を評価しました:1. ゲート領域、2. フローの中間領域、3. フロー領域の終端。フロー長さに即したセルの成長の確認と、セルサイズ予測におけるソフトウェアの精度を確認するためにこの3箇所を評価箇所としました。
評価箇所1 ― ゲート領域:
ゲート位置付近では高圧力が生じるため、セルは小さいままです。SEMの評価によると、解析結果はセルサイズを精度よく予測しています。
評価箇所2 ― フローの中間領域:
フローがゲートから離れるにつれてセルが成長;解析とSEMの双方が同じ傾向を示しました。パーツの中心部分に比べて表面部分ではセルの成長時間が短くなるため、結果としてセルサイズが小さくなります。
評価箇所3 ― フロー領域の終端:
フロー領域の終端部では、材料がすべてのフロー経路を通過することでセルが各方向に成長していきます;一方、低圧力となるフローフロントでは発泡しやすい状態となります。したがって、解析・SEM評価共に大きなセルが形成されました。また、領域内の位置によってセルサイズが異なりました。
4. セル密度の予測と妥当性評価:
MuCell® 技術では、セルサイズだけでなくセル密度も重要な要素です。セル密度とセルサイズ連動しています。フロー長さが伸びて平均セルサイズが大きくなると、フローが占める面積が大きくなり、反対にセル密度が低下します。ここに、解析結果とSEMによる妥当性評価の比較を次に示します。
評価箇所1 ― ゲート領域:
SEMは密度の予測は不向きです。解析結果とSEMを比較すると、解析と実際のパーツにおける密度計算の相関度を確認できます。
全てのゲート領域において、圧力が飽和圧力を超えると発泡しません。発泡はこの領域で起きますが、高圧力によってセルサイズが制限されることで、気泡がつながって大きな気泡にならず、個々に成長することが可能になります(セルの核生成)。このとき、解析とSEMは同じ結果を示しました。
評価箇所2 ― フローの中間領域:
フローが経路を進むにつれて、セルが成長します。セルの成長にともなって面積当たりのセルの数が少なくなり、結果としてセル密度が低くなります。
評価箇所3 ― フロー領域の終端:
フロー領域の終端では大きくなった気泡がつながり、その結果、セル密度が非常に低くなる様子がSEMで確認できます。
結果
本事例を以下のとおり総括します:
- MuCell® 技術はひけの低減が求められるパーツに最適です。従来は最適とされてきた設計(ゲートから離れた位置では板厚を厚くし、リブー壁厚比を高くする)とは異なる設計であっても、ひけの低減可能です。
- MuCell® 技術により反り変形の問題が劇的に改善します。
- 一般的に、フロー長さや平均板厚などによるセルの成長は製品品質の向上に影響します。本事例においても、セルの成長が確認されました。
さらに、上記の重要ポイントはすべてMoldex3D MuCell® 解析で正確に解析・予測されていました。Moldex3D を利用してMuCell® のプロセスをつぶさに調査したProplast社は、その技術の利点を確かめることができました。さらに、MuCell® の技術を用いて顧客に最適なサーフェース品質を提供する際にも、Moldex3Dが大きな助けとなりました。
CAEシミュレーションの価値
“Proplastで培われ活用されたCAEの手法は、MuCell®によるミクロセル射出成形プロセスの正確かつ安定した解析を可能にしました。その結果、パーツ品質・形状向上が可能となったのです。
Moldex3Dを用いて実施したMuCell ®コンポーネントのフロー解析によって、工程パラメーターと全体的な成形品質(軽量化の可能性、体積の低減、ひけ、反り変形)の最適化だけでなく、セル構造の局所ミクロ構造(サイズ、密度、セル分布)の最適化も可能になりました。 ここで取り上げた解析ベースの手法は、目で見て分かりやすく時間の短縮とコスト削減に効果的でありながら、パーツの性能解析(成形可用性、仕様・要求満足度、MuCell ®パーツ品質など)と経済分析(投資、生産性、生産コスト、材料・エネルギー消費量)に適した多くの情報を提供してくれます。
今回ご紹介した事例では、工程パラメーター、MuCell®技術の活用、軽量化、反り変形に関する解析精度の高さが証明されました。”― Proplast社CAE Manager、Andrea Romeo氏
|
Moldex3Dを用いて実施したMuCell ®コンポーネントのフロー解析によって、工程パラメーターと全体的な成形品質の最適化だけでなく、セル構造の局所ミクロ構造の最適化も可能になりました。 -Proplast社CAE Manager、Andrea Romeo氏 |