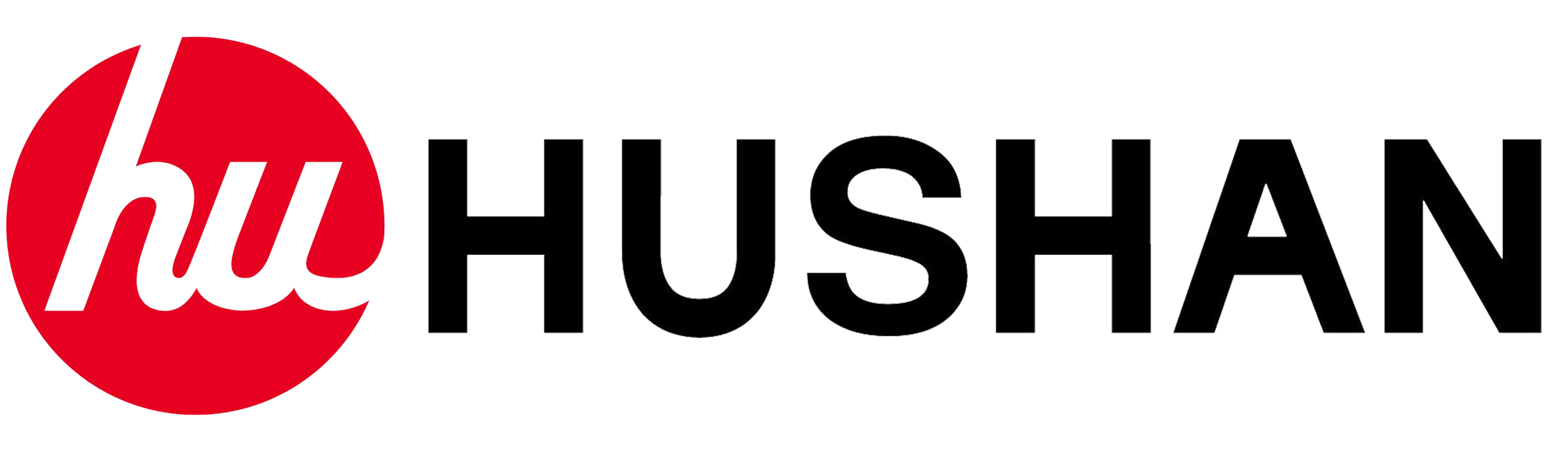
- 顧客名:Hu-Shan Auto Parts Inc.
- 業 種:自動車部品生産
- ソリューション:Moldex3D eDesign
- 地域 :台湾
概要
Hu-Shun社は、ウェルドラインの問題を解決して製品表面の外観をよくする必要に迫られました。そこで、Moldex3DによるCAE解析を行い、製品の厚さとゲート位置を変更することで設計を最良の形を得、ウェルドラインの最短化を実現しました。これにより、製品の強度に影響することなくその外観を飛躍的に向上させました。
課題
- 元の設計では、充填後(End of Filling)にウェルドラインがはっきりと残っていた。(下図参照)
- 製品金型はすでに完成していたため、プロジェクトの主たる目的はウェルドラインの問題解決を低コストかつ短期間で行う事であった。
解決策
Moldex3Dのリアル3D技術を用い製品のメッシュを生成し、ゲート位置と製品の厚みを変更することで製品デザインを向上させました。 修正後、製品部品のデザインは3.0mmから2.0mmに薄型化され、さらに、製品の板厚分布を調整し、シリンダーを空洞化することで、最終的にウェルドラインの長さを9.5mmから4.3mmに短縮することに成功しました。
価値
金型の製造には50万ドルから100万ドルの費用が掛かります。金型の修正には、1回につき5万ドルから10万ドルが必要となります。CAE解析を使えば、失敗によるコストの増大を回避しながら46セットもの製品の設計を変更し、顧客へのコスト転嫁も劇的に減らすことができるのです。
期待されたゴール
- Moldex3Dを用いてのウェルドライン位置の確定
- 設計変更によるウェルドラインの低減
- Moldex3Dを用いての、新規設計作業への適用性の検証
解決策
1. Moldex3Dを使用しウェルドラインを再現
メルトのメルトフロント時間をFig.3に示します。Fig.4が示す通り、ウェルドラインの位置とウェルドライン生成のタイミングによって、その角度と長さが変わります。
Fig. 5 ウェルドライン長と会合角度(Moldex3D導入前デザイン)
2. 問題
- ウェルドラインの問題解決には、ウェルド会合角度が重要で、会合角は、ウェルドラインと密接に関係しています。Hu-Shan社はその豊富な経験から、会合角が90°を超えると分子配向がほぼ同一になり、ウェルドラインは問題にならないことを理解していました。
- 2つのメルトフロントがぶつかる際の会合角を調整し、Moldex3Dを使って正しいメルトフロント時間分布を導き出しました。
3. 結果
ゲート位置や製品の板厚分布などの設計を継続的に変更し、最終的に下図のようなデザインが完成しました。
板厚設計変更:
製品の中央穴周辺に厚みをもたせ、平面の中間部の薄くすることにより、中央穴周辺のメルトフロント流れを加速させます。 この設計で、2つのメルトフロントが平面の縁部でぶつかり、会合角は大きくウェルドラインは短くなります。
傾斜による板厚配分:
傾斜による板厚の変更; これにより、中央穴周辺のメルトフロント流れを加速し製品表面のメルトフロント速度を遅くします。 この設計で、2つのメルトフロントが互いに大きな会合角でぶつかり、ウェルドラインを縮小します。
シリンダー設計変更:
ウェルドラインに近い位置にあるシリンダーを空洞化し、メルトが充填される体積を減らします。シリンダーの設計によって左側のメルトフロントの流れが遅くならないように注意します。
この設計変更によるメルトフロントの結果を下図に示します。
Fig. 12 会合角とウェルドライン長(Moldex3D導入後デザイン)
CAE解析を通じて、Hu-Shan社は板厚分布の変更によってメルトフロント速度を調整し、ウェルドラインの問題を解決できるという結論に至りました。
結果
最終的に、製品の構造、板厚分布、そしてゲート位置変更を行い設計が完了しました。 メルトフロント方向は、板厚分布と構造角度の変更により調整され、この設計変更が、会合角とウェルドラインの長さがに影響を与えました。 Moldex3D導入前のウェルドラインの長さは9.5mmでしたが、Moldex3Dによる解析を経て、ウェルドラインの長さは4.3mmとなり約50%減少しました。
このプロジェクトでHu-Shan社は46セットの製品設計変更を行いました。 これが実際のケースでは、金型ひとつにつき、金型修正には5万〜10万ドル、変更した金型を製造するには50万〜150万ドルの費用がかかります。今回のプロジェクトで変更した46セットについて金型の変更を行った場合には、230万〜460万ドルものコストが必要になったはずです。 また、金型の変更が失敗するとコストはさらにかさみます。CAE解析を活用することで、Hu-Shan社は金型変更の頻度を大きく減らしコストを削減しながらも最良の設計を導くことができたのです。