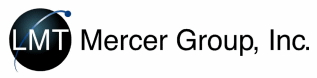
- 顧客名:LMT Products
- 国:アメリカ
- 業種:フェンス、テラスなど
- ソリューション:Moldex3D eDesign
(出典: https://lmtproducts.com/)
概要
本事例の照明製品は、同一原料、同一金型から生産される2つの製品から構成されています。しかし、2つの製品にはサイズ違い、充填が不均衡になるといった現象が発生していました。Moldex3Dを使用することで、これ以外にもある瞬間に型締めトン数が急激に上昇するという問題が検出されました。そのためLMTではランナー、ゲートおよび冷却システムの最適化を行い、不均衡な充填と急激な型締めトン数の上昇という問題を改善しました。また同時に冷却時間を短縮することで、冷却効率と製品平坦度の問題をも改善し、大幅な時間とコストの削減を達成しました。
課題
- 2つの製品は同時に充填が完了しなくてはならない。
- ランナー、ゲートおよび冷却水路の配置に注意し、過度のそりを生じさせてはならない。
ソリューション
Moldex3Dは充填、保圧、冷却、そりに関する分析機能を提供し、充填時間、成形サイクル、冷却効率、製品平坦度の問題を改善するうえで必要なランナー、ゲートおよび冷却システムの設計変更をサポートします。
利点
- 保圧作業終了の際に必要な型締め力が225トンから175トンへと減少したことで、比較的小型の射出成形機を使用することができるようになり、コスト削減につながりました。
- 2つの製品の充填をともに1.28秒で完了することができました。(本来の設計においては大小の製品の充填完了に要する時間はそれぞれ1.28秒と1.07秒でした。)
- 最適な冷却水路の設計を得たことにより、冷却時間を11.99%短縮することができ、冷却効率のギャップは25.452%から13.759%まで縮小されました。
- 小さな製品の平坦度は2.56%、大きな製品については6.18%改善されました。
- 金型製作と品質管理のためのサンプリングにかかるコストを11,500米ドル削減できました。
ケーススタディ
本事例の目的は、金型製作の前にランナーとゲートの設計を最適化し、製品の製造に際して不必要に大きい射出成形機を用いる必要がないようにすることでした。同時に、成形サイクルを短縮し、製品の平坦度を許容範囲内に収め、金型修正と抜き取り検査のコストを削減させることを希望していました。
LMTはMoldex3D eDesignを使用して2つの異なるキャビティの製品メッシュを作成しました。小さな製品はLED基板ホルダーで、大きな製品はリフレクターです。LMTはMoldex3Dのメルトフロー前分析から不均衡な充填を検出し、型締め力、最長冷却時間、不要な冷却水路設計、Y軸変位などを予測しました。
シミュレーション結果に基づいたゲートとランナーの設計変更は図1と図2に示す通りです。
図1 本来の設計(左図)では、小さな製品はサイドゲートを使用し、大きな製品はジャンプゲートを使用していました。設計変更後(右図)、大きな製品は依然としてジャンプゲートを使用していますが、小さな製品は延長されたジャンプゲートを使用するように改められています。

図2 左図の本来の設計と比較すると、右図の設計では大きな製品が元々つながっていたループ状の冷却水路と分割され、
大きな製品の下方に冷却水路を1本追加するように変更されています。
Moldex3Dのシミュレーション結果から、本来の設計では小さな製品の充填に必要な時間は大きな製品よりも短いことがわかります。小さな製品のランナールートを延長する設計変更により、小さな製品の充填時間を大きな製品と同じところまで引き上げることができました。(図3)
図3 本来の設計のメルトフロー前74%(上図)と設計変更後のメルトフロー前96%(下図)を比較すると、
2つのキャビティの不均衡な充填現象はすでに解消されていることがわかります。
この他に、冷却システムを最適化することにより、最長冷却時間は本来の21.009秒から18.489秒に短縮され、それにより成形サイクルも短縮されました。最後に、代表的な陥没現象であるY軸変位の問題についても改善することができました。本来の設計では大小の製品の最大変位量はそれぞれ0.6985 mmと0.1981 mmでしたが、設計変更後の変位量はそれぞれ0.6561mmと0.1930mmでした。
図4 大小の製品のY軸変位の分析結果によると、本来の設計(左)の変位量は設計変更後
(右)よりも大きくなっています。
設計変更の結果は、トライアウト試験によっても実際に確認されました。プロセスエンジニアはMoldex3Dの分析から導きだされた最適なプロセス条件に基づき、実際の射出充填作業の完了前の製品、ショートショットの結果を観察することができます。図5から実際の射出成形の結果とシミュレーション結果が一致していることがわかります。
図5 実際に射出成形された設計変更後の製品から、大小の製品のショートショットとシミュレーション結果が一致していることがわかります。
結論
本事例では生産コストの削減と製品の品質改善の2つの目的を同時に達成し、金型製作前にゲート、ランナー、冷却システムの最適化を行いました。Moldex3Dを使用することで、ユーザーは容易に様々な設計変更を行うことができるとともに、迅速なテストの進行、最適な設計を見つけ出すことができ、実際の射出成形の結果もシミュレーション結果との一致度が高いものになります。ユーザーに金型製作と修正にかかる高額なコストを浪費させることなく、市場への投入時間と品質管理のためのサンプリングをスムーズに進めることができ、大幅な時間とコストの削減が行えます。