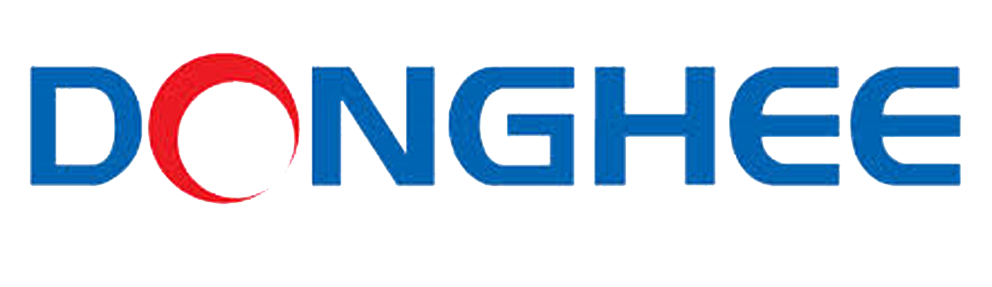
- 顧客名:DONGHEE
- 業種: 自動車
- 導入製品: Moldex3D アドバンスドパッケージ
- 国: 韓国
導入の経緯
DONGHEE Industrial Co. Ltd. はシャーシ、燃料タンク、ペダル、サンルーフ、車軸ハウジング、ボディといった、多様な自動車部品だけを扱っています。同社は自動車部品の品質向上のためにMoldex3Dの導入を決定しました。同社はMoldex3D のシミュレーション結果を元に、ゲート設計を修正し、フレーム部品上のウェルドラインによって引き起こされるクラッキング(亀裂)問題を解決しました。
課題
サンルーフフレーム上に亀裂が入りやすい部分がありました。この問題を解決するために、同社は亀裂の入る場所の特定と、その問題の軽減を行う必要がありました。通常、問題個所を特定するには、構造剛性解析が行われます。しかし構造解析はウェルドラインの影響を考慮することができないため、成形工程の重要な特性が無視されてしまいます。
ソリューション
同社は Moldex3D Advanced パッケージを導入し、事前に問題が発生する場所の特定と最適化を行うことができるようになりました。こうして欠陥を削減し、製品品質を向上させることができました。
ケーススタディ
元の設計には2つのゲートがありました。ウェルドラインは亀裂の入りやすい部分に発生していました。射出成形シミュレーションを実行したところ、ウェルドラインにエアートラップが発生することが判明しました。これが製品剛性に影響し、亀裂を発生する原因と考えられます。また、繊維配向解析結果を調べると、2つのゲートを持つレイアウトではウェルドラインが発生し、剛性に問題が生じることが分かりました。
以上の結果より、3つのゲートを持つ設計が提案されました。修正後の設計のシミュレーション結果ではウェルドラインは発生しませんでした。さらにエアートラップ、繊維配向の結果でも、亀裂の発生部分の剛性は改善されていることが分かりました。このようにして同社はゲート設計を検査するためにMoldex3Dを使用し、ゲートの数と位置を修正することにより、製品の剛性を改良できました。
元の設計(ゲートは2つ)、とそのシミュレーション結果
修正後の設計(ゲートは3つ)と、そのシミュレーション結果
|
|
構造解析で成形特性を考慮しないと、解析結果と実現象では大きなギャップが生じてしまいます(以下のケース1参照)従って、構造解析では射出成形条件を考慮する必要があります。
従って、成形条件を考慮した構造解析(以下のケース2参照)では、ゲート位置がウェルドラインと亀裂に影響を及ぼすことがわかります。さらにゲートの数と位置を変更することが、製品の剛性(強度)を改良し、亀裂発生を回避することがわかります。ゲート設計の調査と最適化にMoldex3Dを使用することにより、同社は開発の初期段階で製品剛性と製品品質を改良することができたのです。