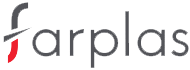
- 顧客名: FARPLAS A.S.
- 国: トルコ
- 分野: 自動車
- ソリューション: Moldex3D eDesign Package / Moldex3D MCM Module
概要
この事例ではPP+GF30 と、エチレン・プロピレン・ジエン・モノマー(EPDM)の流動解析を行いました。このマルチショット射出成形は、非常に難しい作業でした。製品変形の影響をうけながら、グラスファイバーをフロー方向に沿って配向させる必要がありました。もしインサート時に変形した部分の形状が他の部分と正確に合致しなければ、EPDM 充填を行うことはできません。またもう一つの問題は、EPDM をごく薄い層状にして、PP+GF30 上にバランス良く充填することができない点です。ガソリンタンクのケースについて、いくつかのMoldex3D 解析を実行しました。解析結果から潜在的な問題を予測し、適切な修正を行うことで、時間の短縮を図りました。
課題
- PP+GF30 充填後の変形
- ゲート位置とEPDM の流れの断面を修正する
- ホットランナーの量と間隔を補正するのに十分なEPDM 充填量
ソリューション
Moldex3D により、適切な設計修正ができました。第一ショット(PP+GF30)でのそり変形が軽減され、第二ショット(EPDM)ではショートショットが発生しませんでした。メッシュレベルオプションを上げることで、シミュレーションと実験結果が近くなりました (100% 近い精度)。
メリット
製品品質の向上:
- PP+GF30 充填時のトータル変位の軽減
- EPDM 充填時のショートショットを完全に回避
- そり変形挙動および流動挙動のシミュレーション結果と実験結果を比較すると、100% 近い精度で一致
- サイクル時間と開発コストを削減するだけでなく、設計修正にかかる時間も削減できる
ケーススタディ
このケースの目的はマルチショット射出成形(PP+GF30 とEPDM)での問題を解決することです。第一ショット(PP+GF30) によって生じる変形を最小限にし、第二ショットのインサートで形状が一致するようにし、第二ショット(EPDM)のキャビティが適切に設計され、完全な充填を行うことが必要です。
ここでは第一ショットの金型設計を始める前から Moldex3Dを使用し、製品変形が許容範囲内になるような設計を考察しました。次にまだ第一ショットの金型設計が完了していない段階で、第二ショットの解析を実行しました。最後に第二ショットのシミュレーション結果を元に、ショートショット問題を解決するように金型設計を修正しました。このケースでは2つの重要な問題を検出しました。それは 第一ショットのそり変形問題と、第二ショットでの不完全な充填です。第一ショットのキャビティの設計修正 として、特定の部分にリブを追加しました。これにより製品剛性を向上させ、特定部分を削除することで均一な肉厚を実現できました。リブが追加されたことで、第一ショットによる変形が軽減されました。
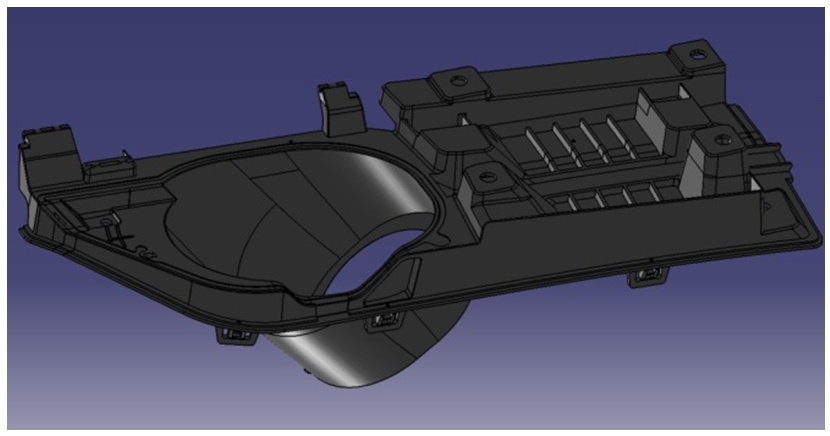
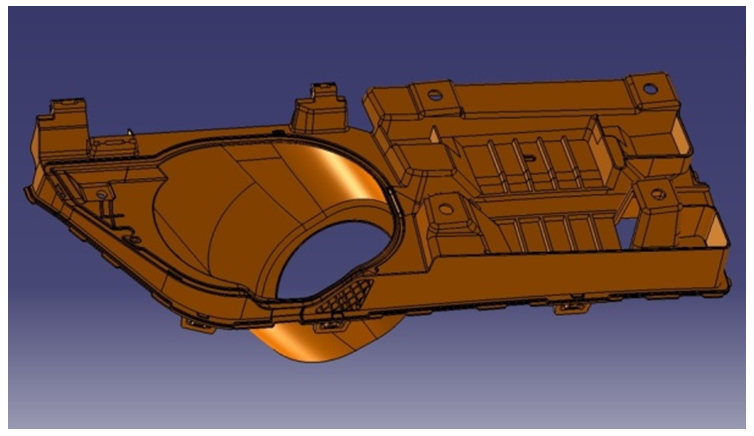
Fig. 1 第一ショットのキャビティの元の設計(左)と、最終製品(右)を比較すると、
最終製品ではリブが多く、いくつかの部分がくり抜かれています。
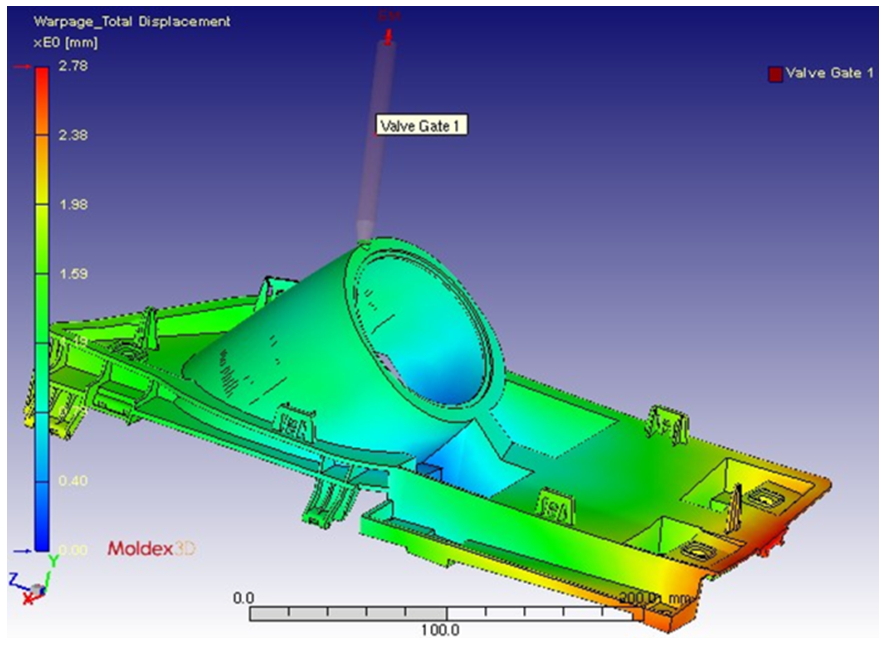
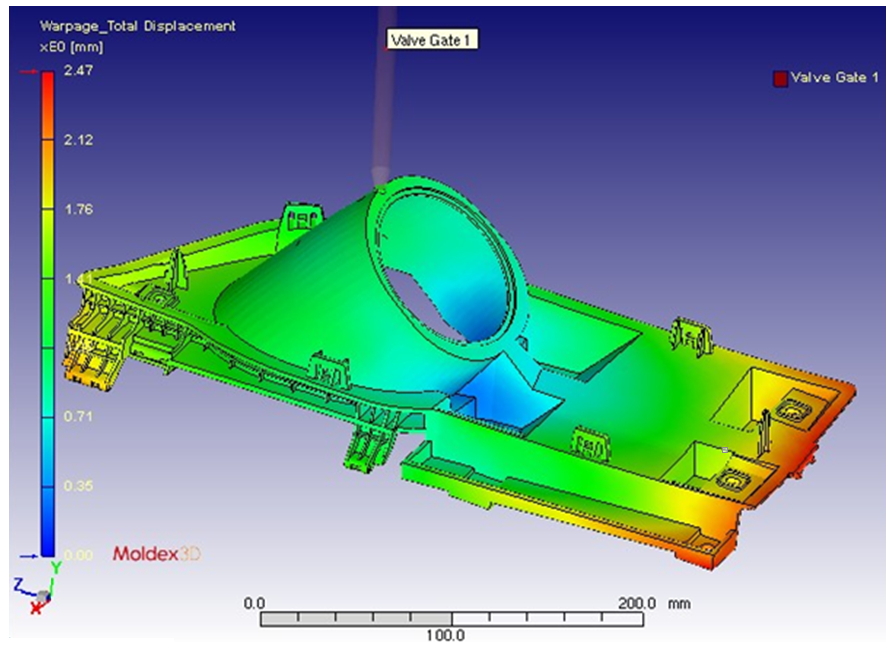
Fig. 2 リブを追加していない元の設計(左)では、リブが追加された改良後の設計(右)に比べて、トータル変位が大きくなります。(元の設計では最大値: 2.78 mm、改良後の設計では最大値: 2.47 mm)
第二ショットのキャビティの設計修正では、ジオメトリ形状と厚みを修正しました。この修正により、 EPDM の充填挙動が改良され、ショートショットを回避することができました。
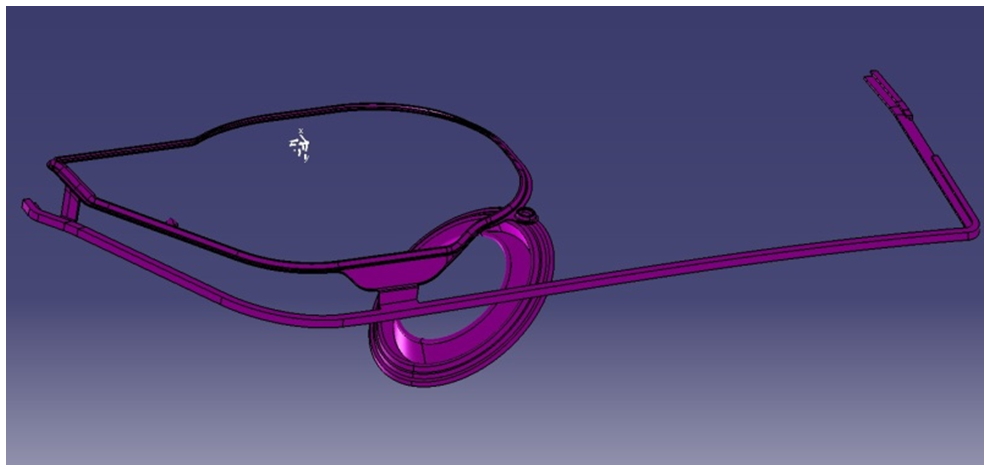
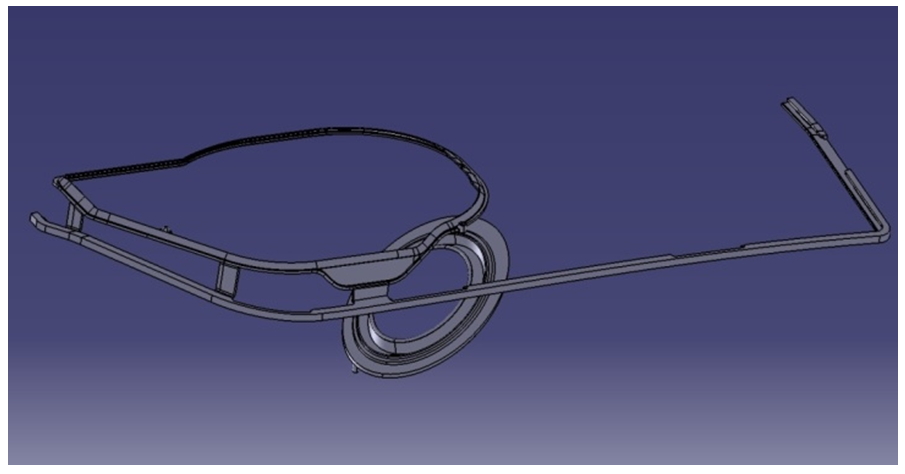
Fig. 3 元の設計の第二ショットのキャビティ形状(左)が修正されました(右)
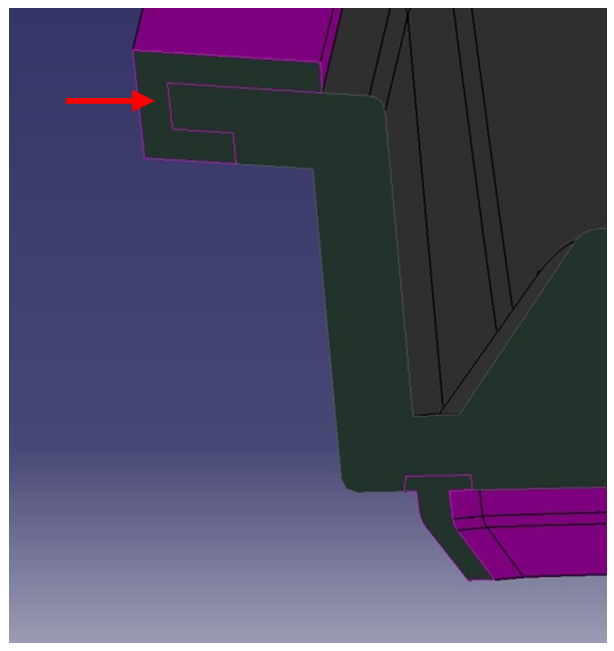
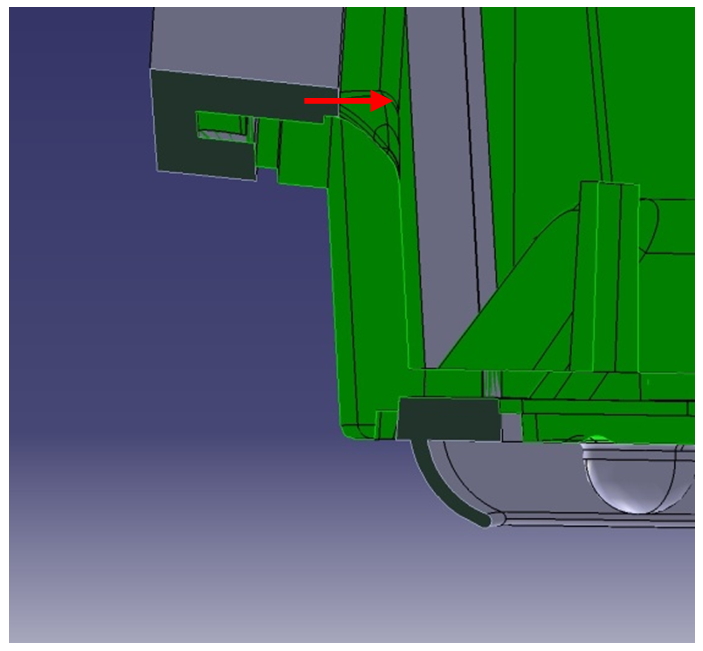
Fig. 4 修正後の設計(右)でのEPDM 注入口の厚みは、元の設計(左)に比べ、大きくなりました。
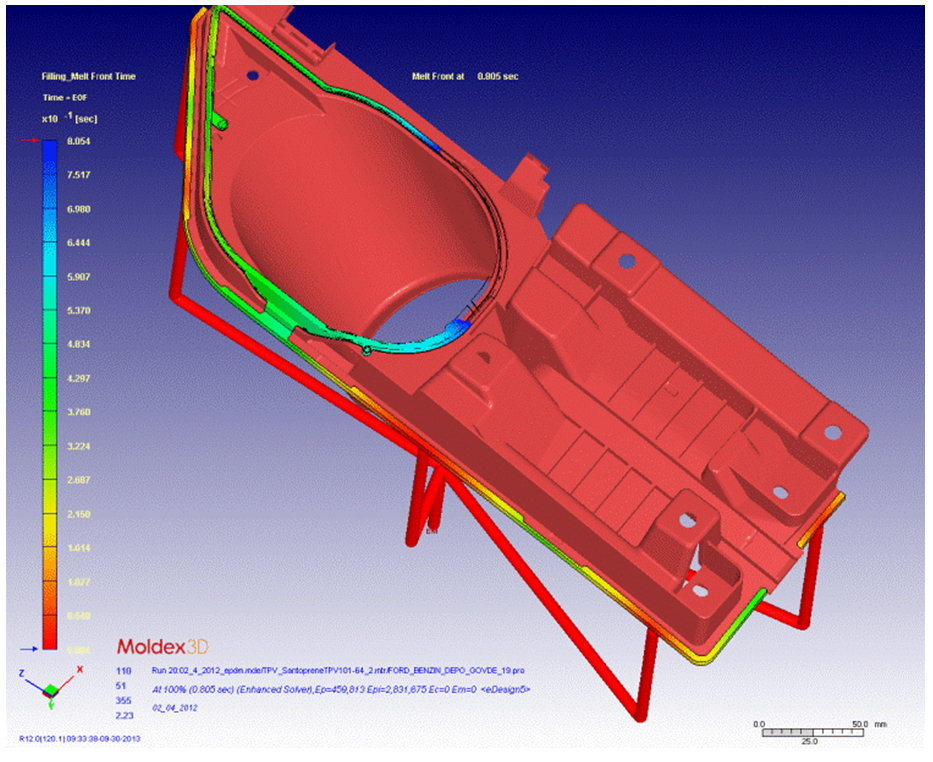
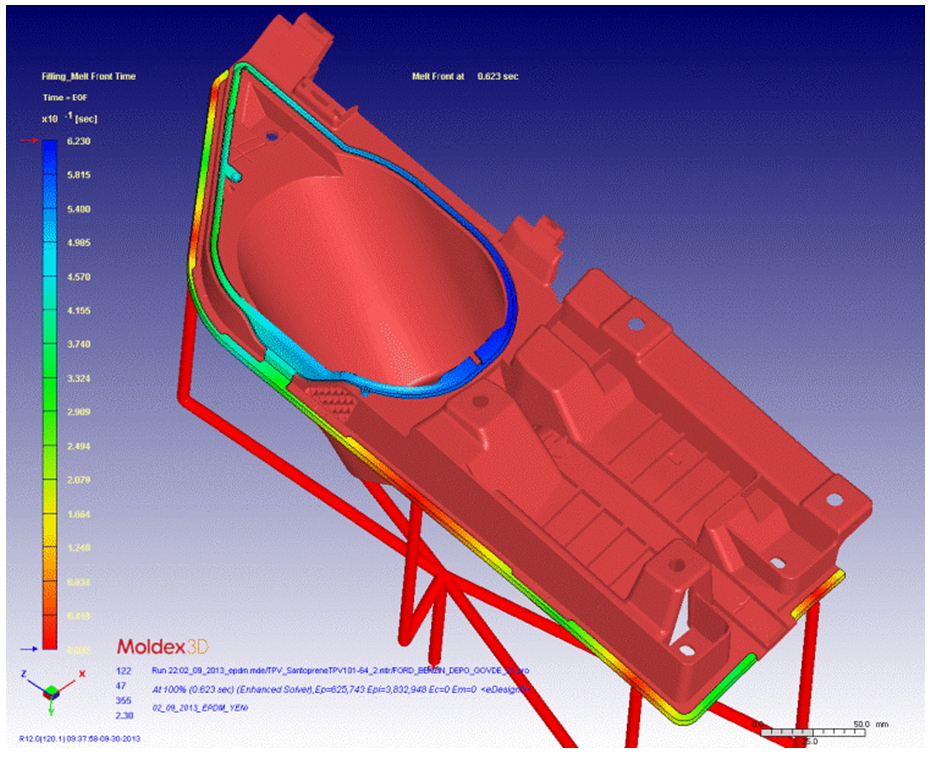
Fig. 5 元の設計(左)のショートショット問題は、修正後の設計(右)では解決されました。
元の設計と修正後の設計を比較、検証します。そり変形が軽減され、ショートショットが回避されたことがわかります。さらにシミュレーション結果を実験結果と比較すると、シミュレーション結果と実験結果が完全に一致することがわかりました。シミュレーション解析でのメッシュレベルを3 から 5に上げると、ほぼ100% の精度で一致しました。以下はEPDM 充填でのショートショット問題の解析例です:
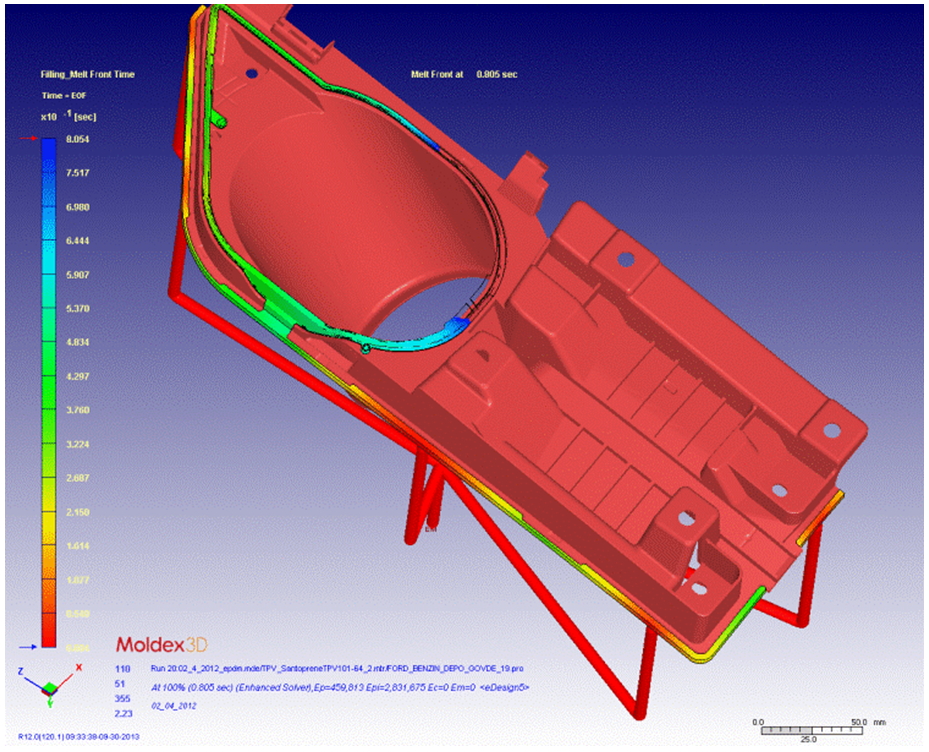
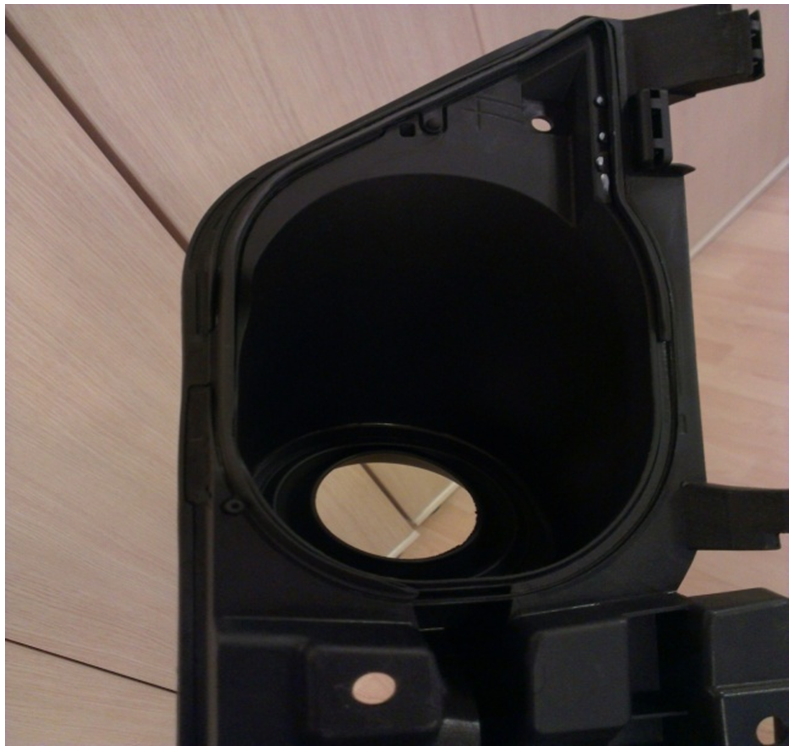
Fig. 6 シミュレーション(左)のショートショット位置は、実験結果(右)と一致しています
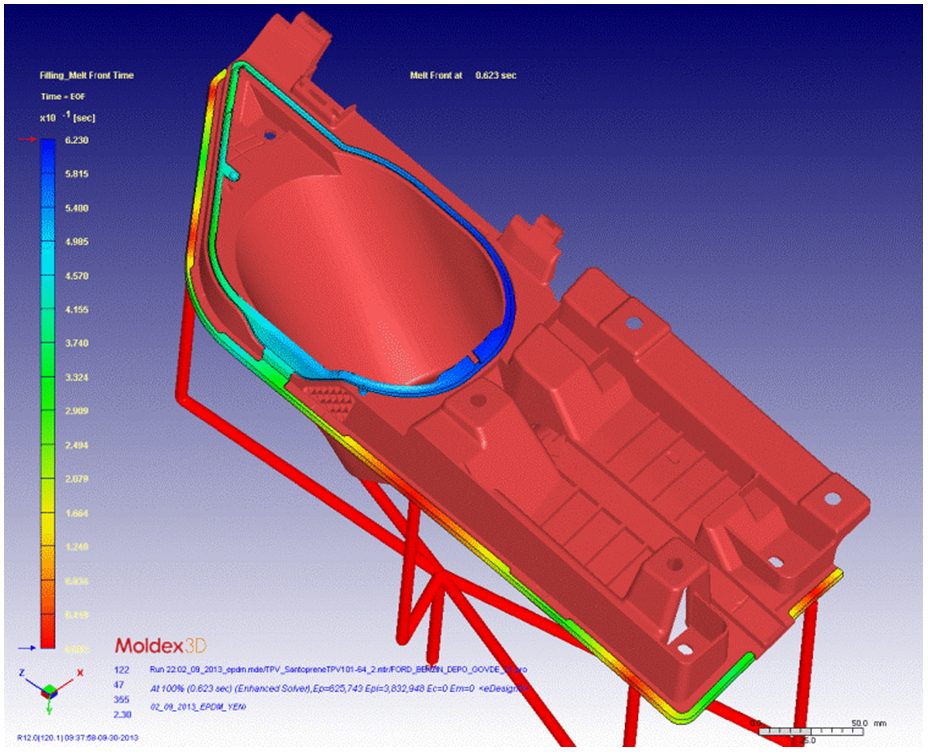
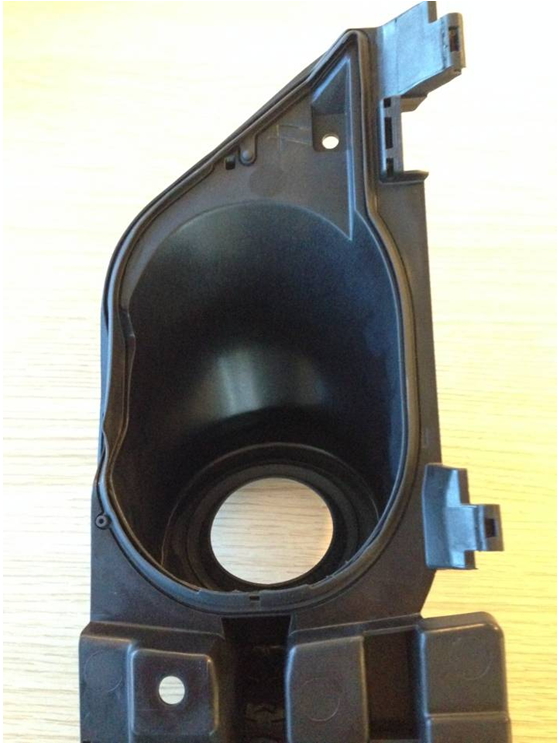
Fig. 7 シミュレーション(左)と実験結果(右)は、両方とも最終製品にショートショットが発生することを示しています
結論
Moldex3D解析を実行することにより、第一ショット(PP+GF30)のそり変形と、第二ショット (EPDM) の流動挙動を理解することができました。シミュレーションモデルのメッシュレベルを5にすることで、シミュレーション結果が実験結果と完全(ほぼ100%)に一致しました。シミュレーションを利用することで、ユーザーは実際の成形を行う前に潜在的な欠陥を予測でき、前もって必要な修正を施すことができます。これにより設計や開発にかかる多くの時間を削減できます。このようにして、 FARPLAS A.S. はマルチショット射出成形での重大な課題を解決することができました。