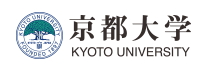
- 顧客名: 京都大学 – 化学工学部専攻
- 業種: 教育
- ソリューション: Moldex3D Solution Add-on / Moldex3D MuCell®
- 国: 日本
概要
京都大学の研究者達は、コアバックを含む発泡射出成形実験を修正し、セル形態と最終製品の成形条件パラメータの効果を明らかにしたいと望んでいました。彼らはMoldex3D MuCell® を利用することで、発泡プロセスで生じる物理現象を理解し、高品質な製品を製造するための適切なパラメータ範囲を検証しました。
課題
- シミュレーションツールを用いた実験結果の解釈
- コアバックの実験用の設計を改良
ソリューション
Moldex3D 微細射出発泡成形ソリューションを利用し、セル形態(セルサイズ・セル密度)およびコアバック発泡射出成形プロセスにおける製品密度について理解を深める。
メリット
- 発泡挙動を予測できる
- 高品質な製品を製造するために必要な適切なパラメータ範囲を決定できる
ケーススタディ
従来の発泡射出成形よりも膨張比が高い製品を製造するため、京都大学の研究者達は新しい発泡射出成形プロセスを設計しました。これはキャビティが完全に充填されてからある一定時間を経た後に、金型の背面を部分的に広げます。このコアバックプロセスにより、厚い製品が低密度で製造でき、さらに使用するプラスチック材料を減らすことができます。研究者達はこの新たなプロセスの実験データを検証するために、Moldex3D MuCell® を選択しました。
この事例の目的は、MuCell® の成形条件パラメータであるコアバック距離や窒素ガス密度の影響、保圧時間とセル形態(セルサイズ・セル密度)の関係を理解することです。京都大学の研究者達は Moldex3D 微細発泡射出成形ソリューションを利用し、コアバックによる発泡射出成形プロセスをシミュレーションしました (Fig. 1)。次に彼らはシミュレーション結果と実験データを比較し、シミュレーション解析結果の精度を検証しました。
Fig. 1 コアバック発泡射出成形をシミュレーションするために使用したジオメトリモデル
京都大学の研究者達は Moldex3D MuCell®を利用し、 3つの成形条件パラメータ(コアバック距離、窒素ガス濃度、保圧時間)の効果を観察することができました。まず解析結果から、コアバック距離が大きくなると最終製品の密度は小さくなることがわかりました (Fig. 2)。コアバック距離を0 mm から8 mmに増やすと、製品密度を30%減少させることが可能です。これは製品重量を30%減らすことが可能だということです。
Fig. 2 3つの異なるコアバック距離の製品密度: (a) 2 mm, (b) 4mm and (c) 8mm.
このようにコアバック距離が大きくなると、セル密度は小さくなります
次に研究者達は、窒素密度が増えるとセルの核生成率が高まり、セル直径が減少することから、セル密度が増えることを確かめました (Fig. 3)。ま保持時間が増加すると溶融ポリマーの固化が進むため、メルト粘度が高くなり、コアバックプロセスの後に気泡が小さくなるか、発泡しないことがわかりました。Fig.4 (左)が示すように、保持時間が10秒以上になると、セル密度が急激に減少することがわかります。Fig.4 (右)が示すように、保持時間が7秒以上になると、ほとんど気泡がないことがわかります。
シミュレーション解析を実行した後、研究者達はシミュレーション結果と実験結果を比較しました。シミュレーション結果は実験結果および実験データとよく一致しました (Fig. 3 & Fig. 4)。
Fig. 3 セル密度とガス濃度の関係 (左)、セル直径とガス濃度の関係(右). グラフより、
シミュレーション結果と実験結果の傾向が一致することがわかります。
Fig. 4セル密度と保圧時間の関係(左)、セル直径と保圧時間の関係(右).グラフより、
シミュレーション結果と実験結果の傾向が一致することがわかります。
結論
京都大学の研究者達は、Moldex3D解析を使って、成形条件パラメータがセル形態と製品密度にもたらす効果を明確に理解することができました。また実験データと比較することにより、Moldex3D シミュレーション解析の精度の高さが検証されました(Table 1)。さらに研究者達は発泡挙動についても予測できました。このような形態学的予測によって得られる情報は、発泡射出成形品の機械特性に関連する有益な情報になります。たとえセル形態がますます複雑になり、予測が難しくなったとしても、シミュレーションツールはセル構造を近似し、安価に提供できます。
コアバック距離 |
セル直径の実験結果 (μm) |
セル直径のシミュレーション結果 (μm) |
セル密度の実験結果 (1/cc) |
セル密度のシミュレーション結果 (1/cc) |
2mm | 85 | 80 | 3 x 106 | 2 x 106 |
4mm | 90 | 95 | 2 x 106 | 9 x 105 |
8mm | 155 | 105 | 1 x 106 | 7 x 105 |