
- 顧客名:RAMCAR Technology Inc.
- 業種:自動車部品製造
- 導入ソリューション:Moldex3D Advanced
- 国: フィリピン
(出典: www.ramcartechnology.com)
概要
RAMCAR Technology社は、自動車・自動二輪車・商用バッテリー製品メーカー向けに高品質の金型・工具・設備機器の製造販売を行っています。 何年もの間、RAMCAR Technology社は産業用機器への投資を通じて社の可能性を広げ続け、業界トップをめざして奮闘してきました。 さまざまな投資の中で最も重要なもののひとつが、射出成形シミュレーションソフトウェア Moldex3Dの導入でした。 Moldex3Dの導入は、同社の生産性を飛躍的に向上させ、最小のコストと時間で最高の品質をもった製品の生産を可能にしたのです。
課題
- 二個取りキャビティとマルチゲート構造における充填アンバランス
- 板厚不均等
- 誤差範囲を超える反り変形
- オーバーパッキングによるバリの発生
ソリューション
Moldex3D CAE シミュレーションソフトウェアを導入し、実機製作に頼らないソフトウェア上での設計上の問題の特定を行い、コストのかかる設計変更の低減と生産性の向上を実現する。
結果
- サイクルタイム:16%の向上
- 生産性:40%の向上
ケーススタディ
パーテーションのピンホールが原因でバッテリーコンテナは、電気分解試験に不合格となっていた。
このケースは、RAMCAR Technology社のバッテリーコンテナを例題とし、Moldex3Dのシミュレーションソフトウェアをどのように設計に活かし、部品製造の最良のアプローチを決定したかを実証しています。
バッテリーコンテナのパーツは不良品率が非常に高く、型電気分解試験を通らない状況でした。 Moldex3Dの解析を使ってパート全体の流れ挙動を可視化したところ、パーテーション上部にピンホール状の穴の存在が明らかになり、それが原因である事が分かりました。
Moldex3Dの充填解析にてパーテーション壁面上部のピンホール発生を確認
製品品質上の問題はピンホールが発端であったことがわかると、製品改良チームは可能な限り短期間でこのピンホール発生を防ぐ手立ての考案を迫られました。既存製品であることから、金型、工具、工程、他のパーツに影響するおそれがあるため、変更は可能な限り少なく小さく抑える必要がありました。
RAMCAR Technology 社の改良チームは、この問題に対して次の4つの解決策を提示しました。
1. パラメータ/工程条件の調整
2. 金型設計の補正
3. 製品設計の変更
4. 金型設計の補正と製品設計の変更
RAMCAR Technology 社が実物のプロトタイプを使って4つの解決策を一つ一つ確認した場合には、多大な時間とコストを費やすことになります。 そこで、同社は、Moldex3Dを活用し、プロトタイプを製作する代わりに、それぞれの解決策をソフトウェアを使い一つ一つ丹念に調べて行くこととしました。 改良チームは、Moldex3Dを活用し最適化したパラメータで各設計変更案の解析を行い、最良の適用アプローチを決定すべく複数の変更案を解析・検討した結果、Moldex3Dの結果が示すゲートサイズの拡張がシンプルかつ最良の変更案であるという結論に至りました。 これにより、射出バランスについての顧客の要望を満たしながらも、問題であったショートショット、ウェルドライン、スカート部のバリ、そして、ひけの最小化が可能になりました。
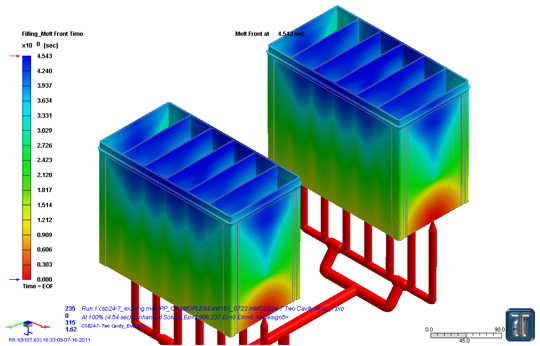
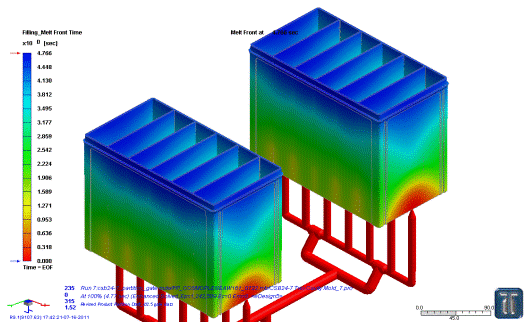
Moldex3Dを用い実際のパーツを製作することなく異なる計変更案の確認・比較しビジュアル化したケース。
問題となった充填遅延(上)と、より均等になったフローパターン(下)のシミュレーション結果。
充填 | 保圧 | 冷却 | 金型開き | 合計サイクルタイム | サイクルタイムの改善率 | |
現行サイクルタイム | 5秒 | 6秒 | 26秒 | 5秒 | 42秒 | 16%の低減 |
調整後サイクルタイム | 5秒 | 3秒 | 22秒 | 5秒 | 35秒 |
既存金型と最適化後の金型のサイクルタイムの比較
サイクルタイム | 製作時間(時) | 生産性改善率 |
現行サイクルタイム: 42秒(2キャビティ |
145パーツ | 41.3%の改善 |
調整後サイクルタイム 35秒(2キャビティ) |
205パーツ |
現行成形と設計最適化後の生産性の比較
低コスト短期間の製品性能向上に成功
Moldex3Dシミュレーションの活用は、射出バランスの調整やバリの発生などのバッテリーコンテナ設計上の問題を解消しただけではなく、RAMCAR Technology 社の全工程の最適化と生産性向上も可能にしました。
Moldex3D導入成果:
- X方向の変位の30% 改善 – 誤差範囲の反り
- 保圧時間の50% 短縮 – 均等な射出の実現
- ピンホール・視認可能な溶接線の解消
- 成形後工程の削減 – バリの解消
- サイクルタイムの16% 短縮による、41.3%の生産性向上
- 電気分解ダイ試験合格
現在、RAMCAR Technology社は、Moldex3D を使って開発コスト削減、開発期間短縮、さらに製品品質の向上を推進しています。 Moldex3Dの予測機能が、プロトタイプの製作と実機試験に代わり、解析による設計評価を可能にしたのです。 現在、RAMCAR Technology社では、商用バッテリー部品などのプラスチックパーツ設計においてもMoldex3Dのシミュレーションを活用する計画が進んでいます。