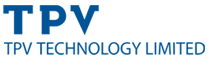
- 顧客名:TPV Technology Limited
- 業種:電子機器
- 導入ソリューション:Moldex3D FEA Interface
- 地域: 台湾
概要
完成したプラスチック製品には、落下試験、熱伝達試験などの所定の試験が行われ、使用目的に耐えうるかが検証されます。 複数の仕様を満たすためには、試験の過程で設計の変更を余儀なくされる場合もあるため、低コストで高品質の製品を作るには実際の製造の前に的確な設計を行うことが必要不可欠です。
本ケーススタディでは、LEDテレビの部品の製品強度の原因追求を行い、その対策と確認を、Moldex3Dと構造解析CAEソフト(Abaqus)と連成させ解決した例をご説明いたします。
詳細
LEDテレビの背面には、テレビスタンドとモニターをつなぐネック部が取り付けられており、製品の組立て中に、接続部にあたるボスにたびたび「き裂」が見られました。(→ Fig. 1)。 この部品は耐荷重性を必要とするため、正確な強度計算に基づく設計が求められていました。
Fig.1 組立中に破損したLEDテレビスタンドのボス
ソリューション
製品強度に与える重大な影響を確認するためにTPV TechnologyがMoldex3Dを用いて充填解析を行ったところ、射出成形部品、特にボスの溶接部に強度不足が発見されました。使用材料データに基づき、樹脂温度30°~140°の範囲にあるフローフロントの会合角の大きさに比例してウェルドライン上の強度不足が顕著になることが解析結果から判明しました。
Fig.2 Moldex3D充填解析によるフロント会合角の再現
さらに、充填解析の結果からボス中心部に10℃の温度差が生じていることも確認されました。このときの温度は溶解温度よりも約10℃低いもので、そのような条件下では、突起部周辺にウェルドラインが発生するのも当然で、二つのフロントの会合角と温度差という条件が相まってウェルドラインの強度が低下していました。
Fig. 3 ウェルドライン形成の原因となった充填温度の差
機構設計の最適化と強度の上昇を両立するため、TPV TechnologyはMoldex3Dを使ってトルク締め工程の応力解析を行いました。解析結果に基づいてき裂発生原因を突き止めると、設計チームはすぐさまピンポイントで設計を変更しました。充填解析結果から、設計チームはボス部のフローフロント会合角の問題だけでなく、中心部の温度条件の問題も発見することができました。さらにMoldex3D FEAインターフェースモジュールを使って、Abaqusに材料特性を出力し応力解析を行い、応力ひずみ図を比較しました。
この解析では、応力のほとんどがロック位置にかかっていたことがわかりました。その最大応力は2.73kgf/mm2に達しており、残留応力は1.59e-03kgf/mm2でした。また、荷重曲線は、ロック位置に33kgfの荷重が作用するとき裂が生じることを示していました。そこで、設計チームはボスの形状を見直し、充填成形解析と応力解析を行いました。設計変更後にTPV Technologyが実施した解析では、突起部の強度が33kgfから40kgfとなり、設計変更前と比べて21%も上昇しました。
Fig.4 Moldex3D FEA インターフェースを用いた最大応力位置の特定
設計最適化前 | 設計最適化後 | 改善率 | |
応力(kgf/mm^2) | 2.72 | 2.18 | 19%↑ |
LE | 1.59 | 1.27 | 20%↑ |
Max Broken force (kgf) | 33 | 40 | 21%↑ |
Fig. 5 設計最適化前と設計最適化後の応力ひずみ曲線の比較
結果
Moldex3DによってTPV Technologyは、コストを抑えながらも生産効率性を向上させました。当初の設計では不良率が30%でしたが、Moldex3Dの解析結果を生かして設計を変更した結果、生産性が10%向上し、年間15万個の生産コストに当たる$41,012(約410万円)のコスト削減に成功しました。TPV Technologyはこの開発プロセスを他の製品にも適用し、Moldex3Dを最大限に活用してさらなる生産性の向上を目指す計画です。
生産性向上率 (%) |
生産能力 (個/年) |
重量 (g) | 材料費 (USD/Kg) | 改良前 (USD) | 改良後 (USD) |
10 | 150,000 | 165.4 | 2.5 | $61,518 | $20,506 |