薄型シェル製品を製造する場合、冷却時の成形条件パラメータを最適化しないと、内部応力が生じることがあります。もし設計者が強度データを考慮せずに、薄型シェル製品を設計すると、構造欠陥や深刻なそり変形問題が発生しかねません。また安全ファクタが大きすぎると、材料の無駄が発生したり、高コストの複雑な構造になりかねません。
2.5D シェルメッシュ生成テクノロジーは、射出成形品の構造解析を実行するため、すでに自動車業界をはじめ様々な業界で利用されています。今までは構造解析での材料特性の重要性は過小評価され、繊維配向、成形温度、残留応力などの影響は考慮されませんでした。このような解析方法では、正確な構造解析シミュレーション結果を得ることはできません。
より正確で包括的な構造解析結果を得るために、製品設計者は射出成形シミュレーションソフトウェアを使って、シミュレーション結果と構造解析を統合しなければなりません。しかし射出成形シミュレーションと構造解析では、メッシュ条件が異なります。構造解析では応力集中領域に重点を置きます。しかし射出成形シミュレーションでは、厚み方向や表面領域に高いメッシュ解像度を要求します。よって射出成形シミュレーションでは、様々なメッシュ要素タイプや密度が要求されます。
Moldex3D はこのような異なる解析ソフト間のマッピング問題を解決するために、3D マッピングシェルテクノロジーを開発しました。Moldex3Dの完全 3D シミュレーションテクノロジーを使えば、3D 射出成形シミュレーションデータを2.5D シェルメッシュ要素に渡し、高精度な解析結果を素早く得ることができるようになります。
設計者はMoldex3D FEA インターフェースのメッシュ生成機能を使い、データとメッシュを出力し、CAE 構造解析プラットフォームに読み込むだけで、構造解析を実行できます。
下の図(Fig. 1)で示したように、設計者は3D マッピングシェルテクノロジーを使って、3D 射出成形シミュレーションの解析結果を2.5D 構造モデルに渡します。次に負荷と境界条件を指定します(Fig. 2)。このように設計者は簡単に、変位と応力分布の解析結果を取得できます (Fig. 3 とFig. 4)。
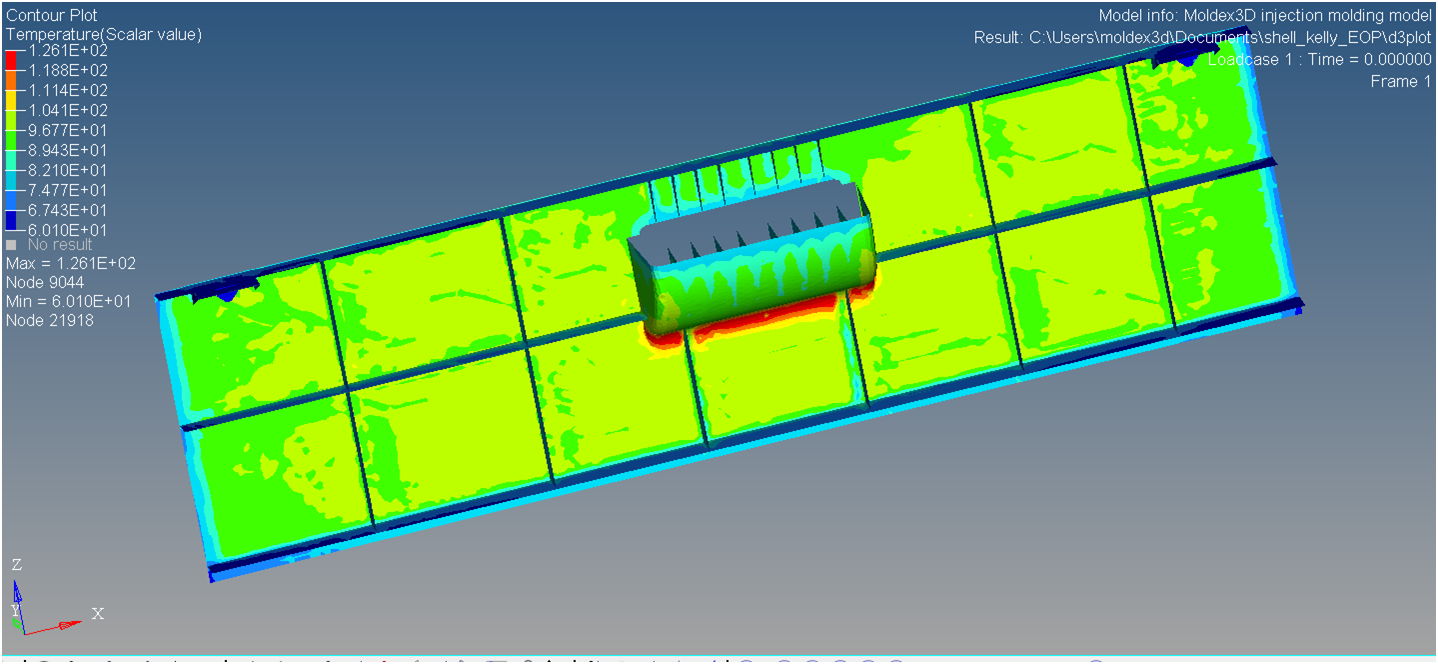
Fig.1 左:3D Moldex3D 射出成形シミュレーションを使った温度分布解析
右: Moldex3D の解析結果を出力した2.5Dモデルの構造解析
Fig. 2 青で囲まれたエリア内の均一負荷を1MPa に設定
Fig. 3 変位分布解析結果
Fig. 4 応力分布解析結果
3D シミュレーションテクノロジーを使えば、2.5D テクノロジーよりも現実に近い解析結果を得られるため、多くの業界で3D シミュレーションテクノロジーが採用されています。設計者が成形プロセスの影響を評価し、製品品質を管理できるようにするために、射出成形シミュレーションと構造解析を統合することが求められています。