
- 顧客名: KOPLA Engineering
- 国: 韓国
- 業種: 自動車
- 導入ソリューション: Moldex3D eDesign / FEA Interface
概要
本事例の製品は自動車のドア部品です。元の製品には深刻な反り変形があり(図1)、組み立てが困難になっていました。この問題を解決し、さらに軽量化を図るため、KOPLA社は金属部品から樹脂部品への軽量化の評価にMoldex3Dを利用して材料特性の違いを解析しました。さらに、Moldex3DのFEA Interfaceから構造解析を行いました(本事例ではANSYSと統合)。その結果、KOPLA社はゲート位置設計の最適化と適切な材料の選定を行い、製品の反り変形と組み立ての問題を解消することができました。
図1 本事例の自動車ドアにみられた深刻な反り変形
課題
- 深刻な反り変形の問題
- 組み立て品質の問題
- 軽量化の目標達成
導入ソリューション
KOPLA社はMoldex3D eDesignとFEA Interfaceを使用して材料特性を検証し、反り変形の問題を解決しました。
利点
- 反り変形の改善に成功
- 射出成形から構造解析までのシームレスなワークフローの実現
- 適切な材料特性の特定
- 金型試作コストの削減
ケーススタディ
本事例における自動車ドア部品は、組み立て要件に基づき多くの穴をもつ設計となっており、ほかの部品と組み合わせるため穴の位置は非常に重要です。そのため、本事例では、製品の反り変形の改善と、組み立て品質の保証が最重要課題でした。
KOPLA社はMoldex3Dを用いて問題を解決しました。適切なメルトフローの確認と潜在的な反り変形低減のため、最初に最適なゲート位置を見つけ出す必要がありました。KOPLA社は反り変形の解析結果(図2)を基にゲート位置の変更を繰り返してゲート位置とゲート形状を最適化しました。ゲート位置決定後、KOPLA社はMoldex3D FEA Interfaceを利用して繊維配向と一部の要素特性を含む反り変形の解析結果をANSYSに出力して構造解析を行い、製品組み立て後の強度と安定性を検証しました。
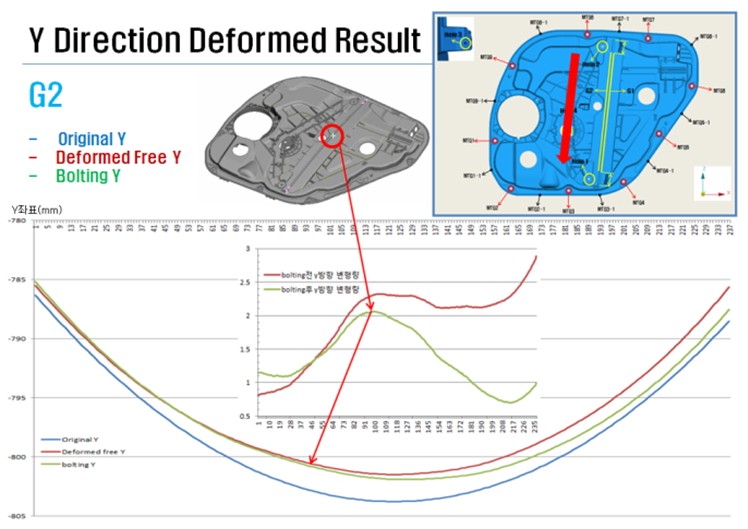
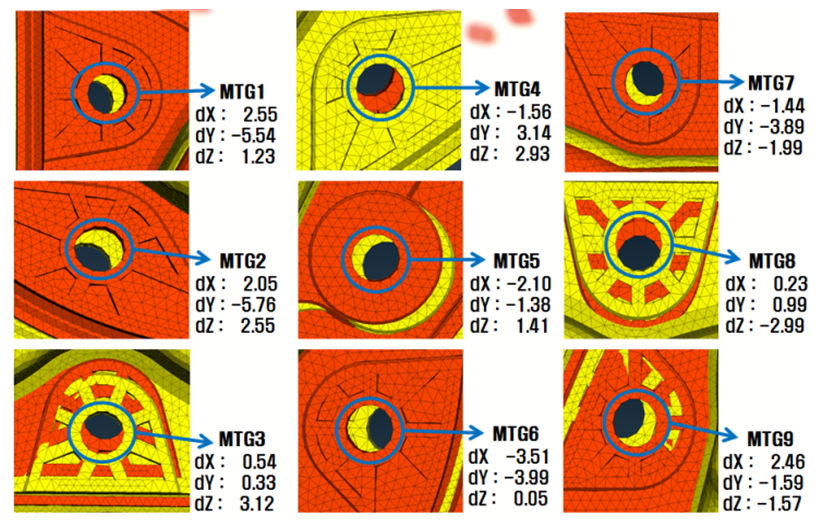
図2 KOPLA社で行ったゲート位置変更と個別の反り変形解析
解析結果から、組み立て時にほかの部品と接する側の平面とは逆方向に向かう反り変形があることが分かりました。そこで、金型の反対方向への変形を利用して補正を行ったところ、組み立てに用いる穴の位置が一致しました(図3および図4)。また、境界条件の設定を変更し、部品組み立て後の変位を確認することで、KOPLA社は変形問題の改善に成功し、製品の構造強度を向上させることができました。
図3 解析結果:変形後のモデルの穴の位置が予想と一致
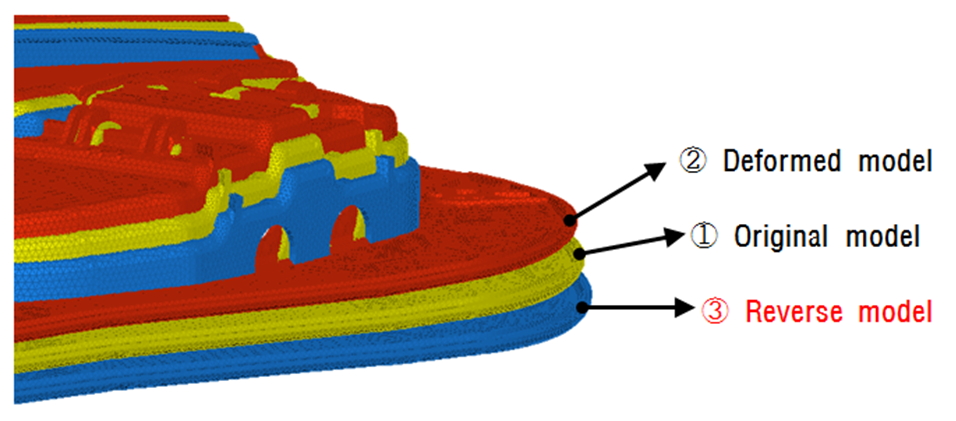
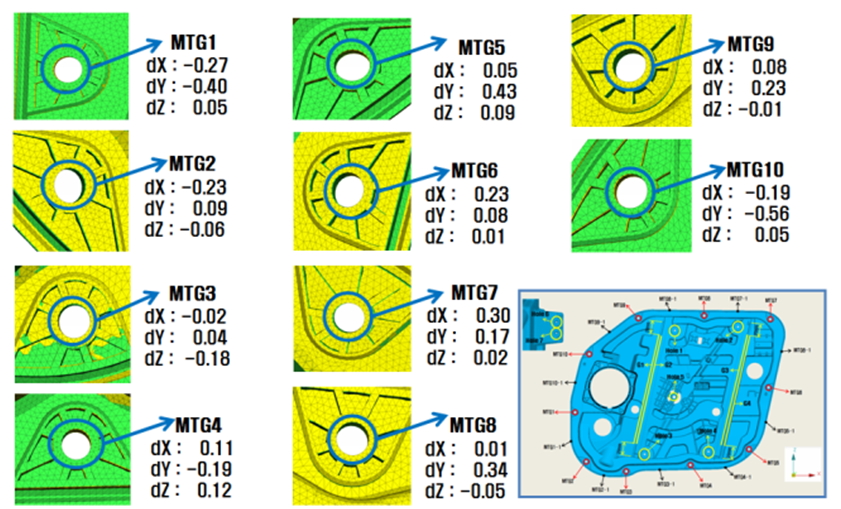
図4 構造解析結果:本事例の製品とほかの部品との組み立て
結論
Moldex3DとANSYSの統合により、KOPLA社は製品の変形と構造設計を改善しました。また、解析結果と実際の製品が非常に高い割合で一致していることが確認できました。このことから、KOPLA社は材料特性を効率的に理解し、適切な製品設計を決定することができました。