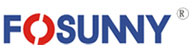
- 顧客名:Fu Chang Electronic Technology Co., Ltd.
- 業種:電子機器
- 国: 中国
- ソリューション:Moldex3D eDesign
概要
コストとエネルギー消費を削減するため、射出成形向けの CAE 技術がさまざまな業界で使用されてきました。Fu Chang も携帯電話ケース、電気通信器機などの製品の製造にCAE技術を活用しています。本事例では、同社がMoldex3D eDesign シミュレーションソリューションを用いて、いかにプラスチック流動挙動を予測し、潜在的な問題を予測したのかについて説明します。シミュレーション解析を行うことで、欠陥問題に焦点を定めることができ、実際の成形の前にゲート設計と冷却回路レイアウトの最適化および成形条件の最適化を行いました。このようにして、同社は材料の削減とサイクル時間の短縮だけでなく、製品品質の改良も成し遂げることができました。
課題
- そり変形
- ウェルドライン
- ストレスマーク
ソリューション
Fu Chang はMoldex3D eDesign を使用して、初期の開発段階で製品設計検証 (Fig 1) と金型設計検証を行いました。Moldex3D の解析結果を元にゲートと製品設計を改良し、さらに最適化された製品設計をシミュレーション技術で解析しました。
Fig 1. 製品設計
ケーススタディ
本プロジェクトの主要目的は、Moldex3Dシミュレーションソリューションを利用してゲートと冷却回路レイアウトと成形パラメータの最適化を実現し、薄肉で軽量な製品における成形問題(流動問題、過剰圧力、そり変形)を解決することです。現在、携帯電話のケースを製造する場合、3-ゲートあるいはマルチゲート設計が一般的です。しかしこのようなゲートでは、不均一な圧力分布が発生し、製品収縮やそり変形を引き起こすことがあります。 (Fig. 2参照) その結果、これらの欠陥を隠すために、ポストプロセス工程が必要になり、製造コストが増加してしまいます。このような形状の製品ではウェルドラインが発生しやすく、それを隠すために厚いスプレーコーティングが必要になります。しかし魅力的な製品外観を実現するためには、このようなやり方はもはや許容できません。また、このようなやり方はサイクル時間を延長することにもなります。
Fig 2. 従来の 3-ゲート設計では不均一な圧力分布が起き (左図の赤丸部分)、ウェルドラインが発生します (右図の赤線)
この問題を解決するため、Fu Chang はMoldex3D eDesign を使用して、最適なゲート設計を探し、元の3-ゲート設計を1-ゲート設計に変更しました(Fig 3)。解析結果では、この修正後のゲート設計は圧力分布を飛躍的に改良し、不均一な収縮によるそり変形問題を解決することができました。さらにウェルドラインも最小限になり、穴の周囲にわずかに発生するのみになりました。これは射出成形工程の後半で、金型温度を上げるように調整することで、完全に解決できます。
Fig 3. ゲート設計に変更することでゲート周囲の圧力が高くなります (左図の赤円)。しかしその他の部分の圧力分布の方がより均一であることがわかります。またウェルドラインが最小限になりました (右図の赤円).
以上のようなゲート設計の問題だけでなく、製品設計問題(不均一な厚み形状)によるストレスマークの発生という課題もありました。同社は 1-ゲート設計を採用することで、厚み変化の大きい領域に移行ゾーンを追加しました (Fig 4)。
Fig 4. 元の製品設計の中心部分は厚みが薄くなっています (左図)。
厚み変化の大きい領域に移行ゾーンを追加しました (右図)。
設計変更を行った後、同社は Moldex3D eDesign を使って元の設計と最適化後の設計をシミュレーションしました。元の設計での解析結果 (Fig5)では、厚み変化の大きな領域で明らかにせん断応力が集中していることがわかります。 これにより、ストレスマークが発生してしまいます。一方、最適化した後の設計では、せん断応力の集中する領域はなく、表面欠陥がうまく解決されたことがわかります。さらに実際に試作品で検証したところ、 Moldex3D によるシミュレーション解析結果と実際の試作品が一致していることがわかります (Fig 6)。
Fig 5 . シミュレーション結果から、元の設計では不均一な厚みによりせん断応力の集中が見られます (左)。
最適化後の設計では、せん断応力の集中は見られません (右)。
Fig 6. 実際に試作品により検証した結果、元の設計では不均一な厚みによりストレスマークが発生しました (左)。
最適化後の設計では、この問題は解決しました (右)。実際の試作品による結果とシミュレーション結果が一致しました。
このようにMoldex3D eDesign を活用することで、ユーザーは異なるゲート設計や冷却回路レイアウトをシミュレーションし、異なる材料や成形条件パラメータ(充填時間、充填圧力、スクリュー位置、冷却温度、成形サイクルなど)を変更して検証することができます。Fu Changは Moldex3D eDesignを活用し、元の設計を包括的に解析し、潜在的に問題が発生する領域を見つけ、問題(ウェルドライン 、そり変形、圧力分布など)の解決案を探し、最終的にサイクル時間や製品品質を最適化することに成功しました。
メリット
最終解析結果から、圧力は20%削減され、そり変形は許容範囲内に収まるようになったことがわかります。さらに詳しく見ると、X-軸方向の変位は 50%、Y-軸方向の変位は55%、Z-軸方向の変位は 30% 改良されたことがわかります(Fig 7)。薄く、軽量な製品を製造する上での課題は、ウェルドラインや表面欠陥、バランスの悪い圧力分布などですが、これらの問題をうまく解決することができました。この改良によりポストプロセス処理が不要になったため、サイクル時間の短縮や製造コストの削減などが実現できました。
Fig 7. Z-軸方向の変位 (左)が、最適化後の設計では改良されました (右)
Fu Chang は Moldex3D eDesign を利用して複数の設計変更をすぐにシミュレーションすることで、設計段階で製品設計や成形条件を最適化することができました。シミュレーションを使うことで潜在的な製品欠陥を予測し、前もって欠陥を回避することができます。 こうして製品品質を飛躍的に改良し、製造コストを削減することが可能になります。この事例から、Moldex3Dが製品最適化と設計検証に最も信頼できるツールであることがわかります。