- 顧客名: DURA Automotive Systems
- 国名:インド
- 業種:自動車部品生産
- 導入ソリューション:Moldex3D Advanced Package; Flow, Pack, Cool, Warp, Designer BLM, Viscoelasticity
DURA Automotive Systemsは世界的なサプライヤーとして、自動車設計と自動車工学に精通しており、革新的なソリューションで自動車産業の発展を支えています。100年を超える研究開発の歴史をもつDURA社は、革新的かつ総合的な電子システム・軽量化ソリューションを生み出すサプライヤーとして大手自動車メーカーから厚い信頼を寄せられています。(出典:https://www.duraauto.com/)
概要
当事例では、車のウインドウのエッジピースを取り上げます。エッジピースは透明なガラス、ガラスラン・チャネル(GRC)、アルミはめ込み具の3つの部品で構成されています。このうち、GRCの変形が原因で製品のギャップとフラッシュの仕様を満足できず、組み立てが困難になっていました。DURA Automotiveのエンジニアは、変形の原因を特定するためにMoldex3Dを利用しました。その結果、PVCの厚い壁とGRCの接触が製品機能に問題を起こしていることを突き止めました。そこで、DURA Automotiveのエンジニアは、強度を維持したまま製品の厚みと変形を減らすため、ABS製はめ込み具を採用しました。その結果、DURA社はMoldex3Dの解析結果に基づいてツールを改良することで最適設計を導き出し、反り変形の解消、および組み立ての問題を解決しました。
課題
- 反り変形に起因する組立困難
- ヒケ
- 冷却時間の短縮
導入ソリューション
DURAは反り変形、冷却、ヒケの問題を解決するため、Moldex3Dを利用してGRCの設計改良を検証しました。
メリット
- 流動バランス改善
- X方向変形量の80%低減、ギャップとフラッシュの仕様満足、スムーズな組立
- ヒケの解消
- 冷却時間の66%短縮
- 開発サイクル短縮
ケーススタディ
本事例では、ウィンドウのエッジピースにおいてギャップとフラッシュの仕様を満たす必要がありました。当該製品は透明なガラス、ガラスランチャンネル(GRC)、アルミ製はめ込み具の3種類のはめ込みパーツで構成され、またPVC材料で覆われています(Fig. 1、Fig. 2)。GRC付近のPVC板厚が変形の原因ですが、この厚みを減らすと製品の組み立てが困難になります。
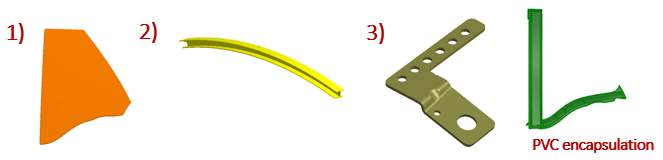
Fig. 1 エッジピースのはめ込みパーツ:(1)透明ガラス、(2)ガラスランチャンネル(GRC)、(3)アルミ製はめ込み具
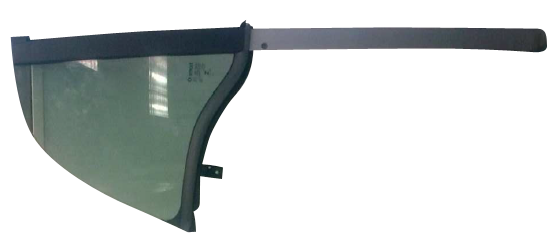
Fig. 2 実際の組立図
成形後の収縮と冷却が不均一であることが原因で、GRCはX方向に5 mm変形していました(Fig. 3)。そのため、GRCはギャップとフラッシュの仕様を満たせず、組み立てにも問題が生じていました。そこでDURA社は、Moldex3Dを用いて問題の関連性を解析し、GRCの変形の原因を特定しました(Fig. 4)。
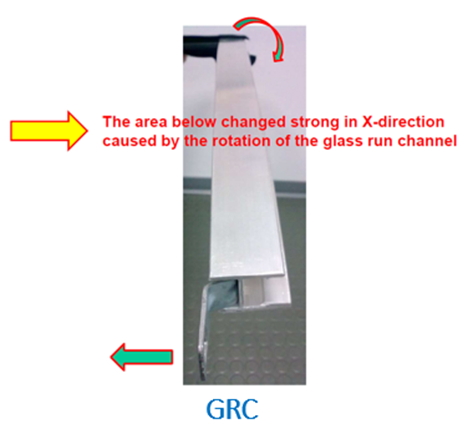
Fig. 3 GRCの変形
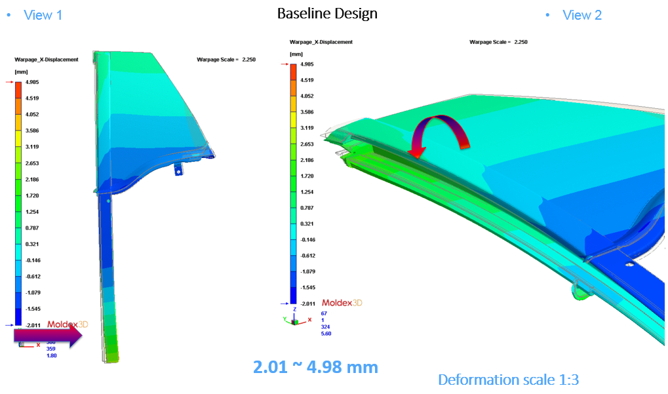
Fig. 4 Moldex3D反り変形解析の結果:GRCがX方向へ5mm変形
Moldex3Dによる解析から、反り変形の原因を確認できました。この問題には、大きく分けて次の4つの原因がありました:GRC付近のPVC板厚が不均一(Fig. 5)、冷却終了時に生じるホットスポット(Fig. 6)、製品の不均一な収縮、冷却時間の不足。さらに、冷却終了時に発生するヒケも問題でした(Fig. 7)。
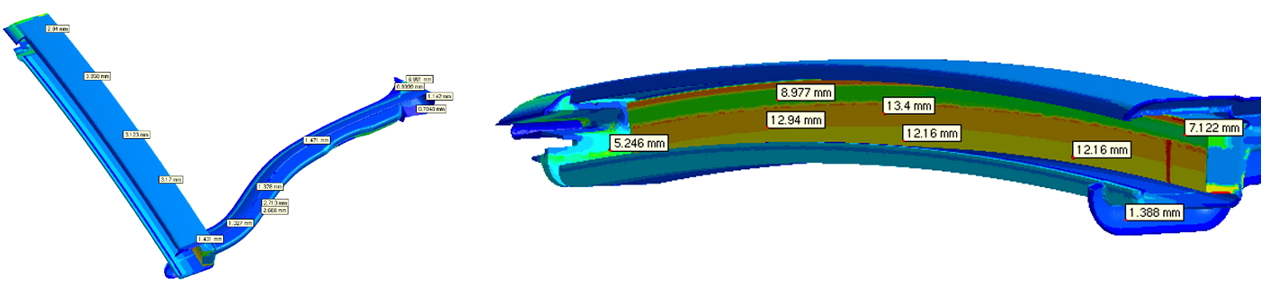
Fig. 5 不均一な板厚:製品の厚みは場所により0.5 mm ~13.4 mmと大きく異なる
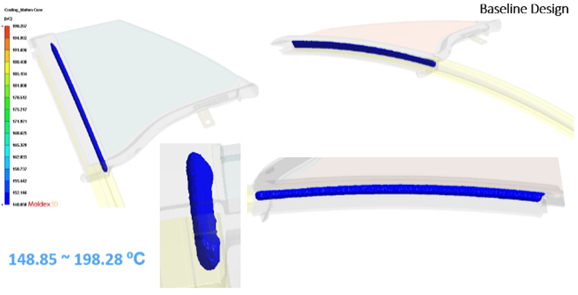
Fig. 6 プラスチック溶融エリア: 製品の冷却終了時で中心部は未固化(青色部分は冷却終了時点でまだ固化していない事を表す)
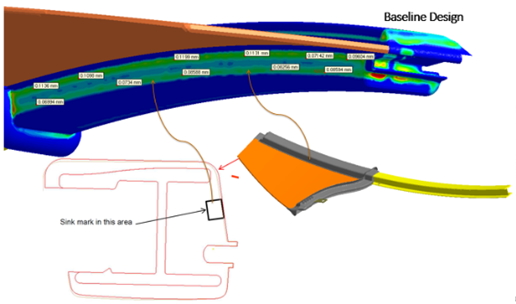
Fig. 7 冷却終了時に発生したヒケマーク:最大0.1 mmの深さ
DURA社は製品設計とプロセスパラメーターの修正による変形問題の解決を目指しましたが、ギャップとフラッシュの仕様を満足することはできませんでした。ABS製はめ込み具を1つ追加すると、製品の厚みや部品強度に影響することなく変形を解消できました(Fig. 8、Fig. 9)。また、DURAはMoldex3Dを使って設計変更の検証も実施しました。
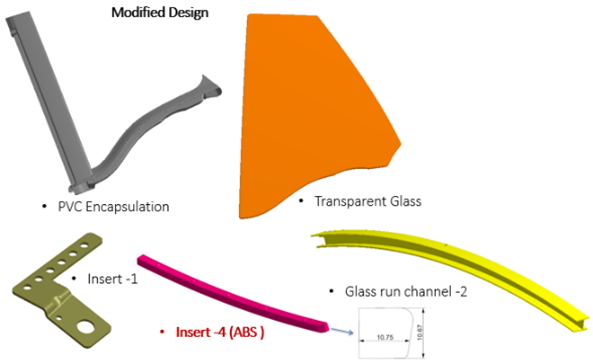
Fig. 8 修正後の製品設計
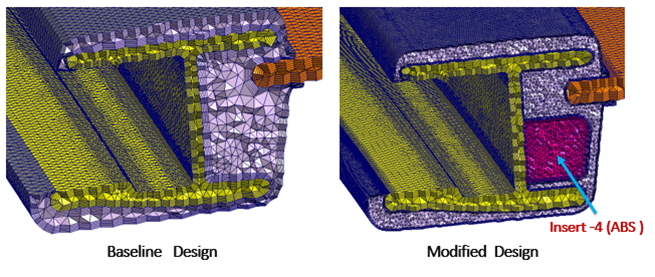
Fig. 9 当初の設計とABS製はめ込み具を追加した設計
Moldex3Dの解析によって、反り変形の問題を解決し(Fig. 10、Fig. 11)、また、組み立ての難題も解消しました。必要な冷却時間も112秒から38秒に短縮され(Fig. 12、Fig. 13)、ヒケの問題も解決しました(Fig. 14)。
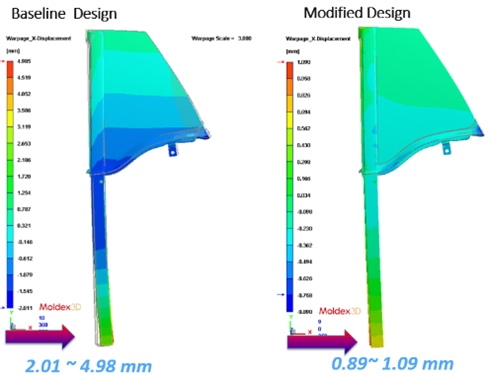
Fig. 10 設計修正後、X軸方向の反り変形が5 mmから1 mmに縮小
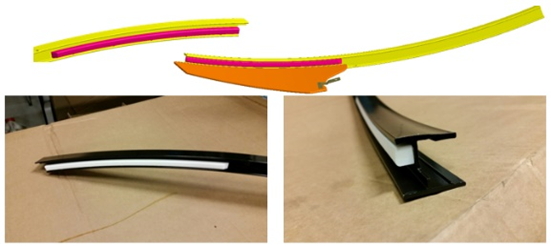
Fig. 11 実際の組立図。ABS製はめ込み具の追加により、X軸方向の反り変形が1 mmに縮小
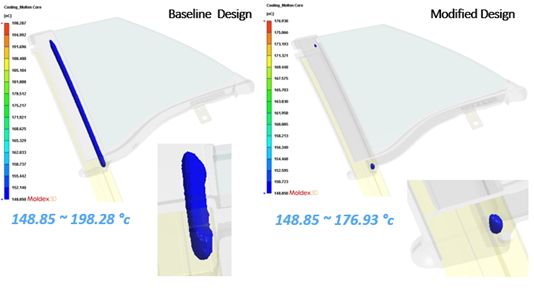
Fig. 12 プラスチック溶融エリア。ABS製はめ込み具の追加後、中心部の未固化問題は大幅に改善

Fig. 13 ABS製はめ込み具の追加後、必要な冷却時間が短縮され、35〜40秒で十分突き出し温度に到達
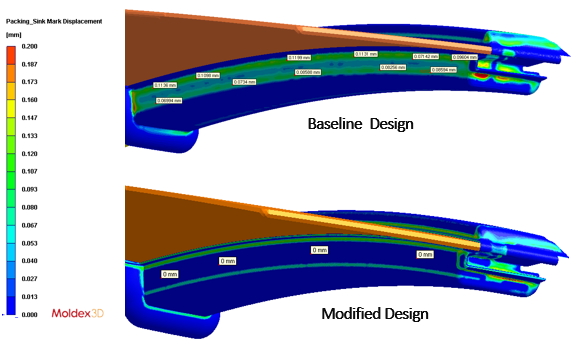
Fig. 14 ヒケが0.1 mmから0 mmへ改善
結論
DURAはMoldex3Dを用いて製品の設計変更プランを検証し、ABS製はめ込み具を肉厚箇所に置くことで、製品強度を維持したままGRCの厚さを85%近く減らせることがわかりました。Moldex3DのサポートによりDURA Automotiveは変形に影響する原因を特定することに成功しました。さらに、最適化後のデザインは反り変形、ヒケを効果的に低下させ、成形サイクルの短縮を実現しました(表1)。