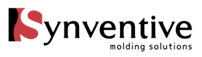
- 顧客名:Synventive Molding Solutions
- 国:アメリカ
- 業種:ホットランナー
- 導入ソリューション:Moldex3D Advanced
概要
一般的に、シーケンシャルバルブゲートシステムは、ウェルドライン発生回避を目的として大型の射出成形品の製造に用いられています。しかし、この技術を用いて製造する際に、未着色の製品にしばしばストレスマークが発生し、塗装の乾燥後に光沢の不均一といった問題が見られることがあります。また、ゲートノズルの反対側にはホットスポットが表れる場合もあります(Fig. 1)。Synventive社のアクティブゲートテクノロジーは、従来のスイッチ制御によるバルブゲート式ホットランナーシステムと比較すると、バルブピンのストローク、速度、加速度などの制御を網羅した、より先進的な制御システムとなっています。この高度な制御システムをMoldex3Dで解析することで、射出成型メーカーは製品不良の予測と対策を行うことが可能です。
Fig. 1 標準的なシーケンシャルバルブゲートによく見られる成形不良
課題
- シーケンシャルバルブゲートの利用による製品の成形不良
- 新たな金型製作や修正を行うことなく、成形不良問題を解消
- ソリューション
Moldex3D Advancedを利用して標準的なシーケンシャルバルブゲートシステムの解析を行い、成形不良を特定することができました。また、バルブピンの動作制御を解析し、プロセスを最適化(シーケンシャルバルブゲートシステム)することにより、製品の成形不良問題を解消することに成功しました。
利点
- 一般的な製品不良の早期発見
- アクティブゲートテクノロジーによる検証に基づく製品不良の解消
- コスト、時間、不良率の削減を達成
ケーススタディ
このプロジェクトの目的は、標準的なシーケンシャルバルブゲートシステムにおいて生じる成形不良、および成形不良が発生する可能性のある箇所を正確に特定することにあります。また、Synventive社は研究開発中のバルブピン動作テクノロジー(シーケンシャルバルブゲートシステム制御)-アクティブゲートをMoldex3Dで解析し、製品不良問題解消に役立てています。
本事例では、バルブゲート式ホットランナーシステムを2つ備えた2つのキャビティ設計を紹介します(Fig. 2)。溶融材料が第1ゲートのバルブピン(Drop 1と3)から第2ゲートのノズルを通過した後、第2ゲートのバルブピン(Drop 2とDrop 4)が最高速度で開放されます。このとき、高圧圧縮されたプラスチック材料が第2ゲートのノズルからキャビティ内に射出されます。ソフトウェアが予測した潜在的な問題の1つは、メルトフロントの速度が第1ゲートのノズルからのものよりも速いことです。メルトフロントが非常に大きく、第1ゲートとの差が顕著であることが等高線から確認できます。このような場合には、ストレスマークが発生しやすくなります。2つ目の問題はプラスチック材料が逆流することにより、一部の密度が非常に高くなることです。これは、等高線間隔が小さいことから確認できます。以上の問題により、製品側面においてメルトフローの遅滞が生じています(Fig. 3)。完成製品の外観は一見すると問題がないように思われますが、製品の塗装が乾燥すると、溶融密度の高い部分の収縮とそのほかの部分との差により、光沢が不均一になります。このほかにも、溶融材料が高圧でキャビティ内に進入することにより、キャビティ内で硬化したプラスチック材料が再溶融し、ホットスポットが発生しやすくなります。
Fig. 2 ホットランナーシステムの設計
Fig. 3 変更前のシーケンシャルバルブピンの動作設定によって生じる制御不能なメルトフロント
そこで、Synventive社は第2セットのノズルのバルブピンの開放速度と加速度を制御するため、設定を変更しました。第2ゲートのノズル(Drop 2とDrop 4)は最高速度での開放は行わず、6.35秒に速度を制御することで(Fig. 4)、第2ゲートのノズルとシステム全体との圧力差を縮小しました。これにより、第2ゲートのノズルからのメルトフロントが第1ゲートを大きく超えることはなくなり、またプラスチック材料の逆流、高密度部分の発生、ゲートの反対側部分のプラスチック材料の再溶融などの問題を解消しました。設計変更後、解析結果から製品全体の等高線が均一になっていることが確認できます(Fig. 5)。
Fig. 4 変更前の設計と最適化された設計における高速、低速のシーケンシャルバルブゲートの動作設定
Fig. 5 制御されたメルトフロント:最適化後のシーケンシャルバルブゲートの動作設定
シーケンシャルバルブゲートシステムの制御を行った後(バルブピンを低速開放することにより、プラスチック材料のキャビティ注入を制御)、Synventive社は3つの射出成形品(シートバック、グローブボックス、ドアパネル)を製造し、製品品質の改善を確認するために従来のプロセスとの比較検証を行いました。その結果、従来のプロセスで生じていた製品不良が解消されたことが確認できました(Fig. 6)。
Fig. 6 実際に製造された製品の解析結果の検証
結論
Moldex3Dを利用することで、Synventive社は金型製作前に標準的なバルブピンの動作設定における潜在的な問題を特定しました。高度なバルブピンの動作制御については、その解析結果を元にシーケンシャルバルブゲートの設定を変更してメルトフロントの制御と製品不良を解消し、さらに、不良率を引き下げることで、時間とコストの削減を実現しました。