- 顧客名:高雄応用科学大学 プラスチック精度研究所 (PPL)
- 地域:Taiwan
- 業種:研究 & 教育
- 導入ソリューション:Moldex3D eDesign / 射出圧縮成形 (ICM) モジュール
概要
自動車のヘッドライトレンズは、かつては複雑で高価なガラスで作られていました。現在、ガラスに代わって、プラスチック製品が用いられてきています。しかしヘッドライトレンズの形状は厚みが不均一であるため、従来の射出成形方法ではコアと表面層の間の熱放散が不均一になり、そり変形問題が発生しやすくなります。このそり変形問題を解決するには、従来の射出成形方法ではなく、射出圧縮成形(ICM) を用いることが解決策となります。このケースでは、PPL はMoldex3D の射出圧縮成形(ICM) シミュレーション機能を使い、自動車用ヘッドライトレンズにICM を採用することの可能性を調査しました。またこのシミュレーション結果を元に、成形工程の最適化のための成形条件を調査しました。Moldex3DのICM シミュレーション結果から、PPLは ICM 工程を完全に理解し、ヘッドライトレンズの成形にICM を採用することの利点(安定性、大量生産、時間とコストの削減)について確信しました。このようにして Moldex3D シミュレーション解析を元に、PPLは射出圧縮成形(ICM)がヘッドライトレンズ製造に適していると証明しました。
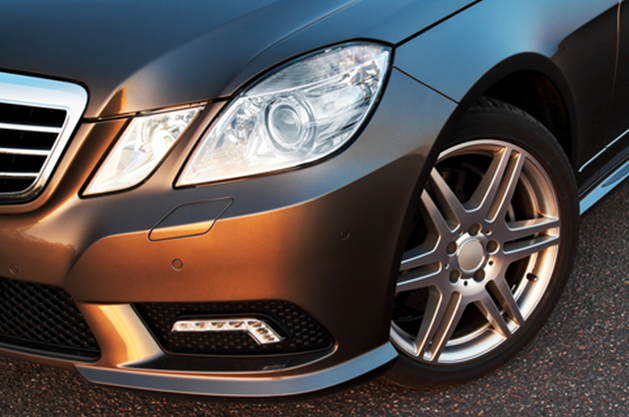
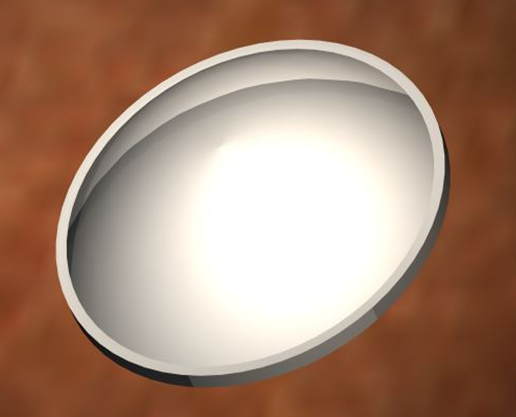
Fig. 1: ヘッドライトレンズ Fig. 2: 製品設計
課題
- 貧弱な光学特性
- そり変形問題
- 著しい体積収縮
![]() |
![]() |
|
Fig. 3: Moldex3D 解析結果からコア部分の製品収縮が顕著であることがわかります。これは不均一な厚みと熱放散が原因です。 |
Fig. 4: Moldex3D 光学解析結果から、ゲート位置に残留応力が集中することがわかります。 |
メリット
Moldex3D シミュレーション解析と実際の試作品を作成した結果、PPL は射出圧縮成形(ICM) が製品品質を改良する解決策であるという結論に達しました。
- 製品収縮は44%改良されました。
- そり変形は29%改良されました。
- フリンジパターンがより均一になり、ゲート部分の残留応力の分布が均一になりました。製品の光学特性は飛躍的に改良されました。
ケーススタディ
PPL は製品品質の改良のために、従来の射出成形工程の代わりに、射出圧縮成形 (ICM) を採用することを決定しました。
ヘッドライトレンズの成形にICM が良いと判断された理由:
1. 射出圧力(トン数)の減少
2. 残留応力の減少
3. 分子配向の減少
4. 均一な保圧圧力により収縮を軽減
5. ヒケとそり変形を軽減
6. 複屈折性能の向上
7. 特定の体積変化が可能
8. 製品寸法精度が向上
このケースの目的は、Moldex3D射出圧縮成形モジュールを使ってヘッドライトレンズ製造にICM を採用できるか判断することです。このケースは3つの重要な要因に注目しました: そり変形、体積収縮、光学特性。また従来の射出成形と射出圧縮成形(ICM)の比較を行いました。シミュレーション結果と実際の試作品を比較した結果、ICMの利点が確認され、製品品質においてもICM が優れていることがわかりました。
まずPPLはMoldex3D そり変形解析を実行しました。従来の射出成形法では不均一な製品厚みにより、コアと表面レイヤー間の熱放散が不均一になり、欠陥(そり変形、残留応力集中)が発生しやすいことがわかりました。ICM を採用すると圧縮時のキャビティ全体の保圧圧力が均一になり、必須射出圧力が小さくなることがわかりました。このことは不均一な圧縮分布によって生じるそり変形を飛躍的に軽減する利点となります。Fig. 5 と Fig. 6 は、最大そり変形量が0.7mm から0.5mm に軽減したことを示しています(改良率: 29%)。
![]() |
![]() |
|
Fig. 5: 射出成形工程-そり変形最大値は約0.7mm (ゲートとコールドスラグウェルを除く) |
|
Fig. 6: 工程-そり変形最大値は約0.5mm (ゲートとコールドスラグウェルを除く) |
Moldex3D のシミュレーション結果から、製品のコア部分に熱が集中し、体積収縮が高レベル(12%)であることがわかります。このことから、従来の射出成形法では、深刻な収縮欠陥が発生することがわかります (Fig. 7)。それとは対照的に、ICM 工程ではコア部分の温度分布が均一であることが確認でき、 体積収縮が44%も改善することがわかります。
![]() |
![]() |
|
![]() |
![]() |
|
Fig. 7: 射出成形工程-コア部分の収縮率は12.1% (上部). 実際の製品の体積収縮は -862.4µm (底部). |
|
Fig. 8: ICM 工程-最大収縮率は9.96% (上部).実際の製品の体積収縮は -490.5µm (底部) |
またフリンジ間ターン解析を比較すると、 ゲート領域に顕著なフリンジパターン(貧弱な光学特性)が発生することがわかります (Fig. 9)。しかし ICM 工程では光学特性が飛躍的に改善されます。これは金型内部圧縮により圧力が低くなり、ゲート付近の残留応力が均一に分布しているためです。 (Fig. 10).
![]() |
![]() |
|
![]() |
![]() |
|
Fig. 9: 射出成形工程-ゲート部分(上部)に顕著なフリンジパターンが観察されます。光弾性応力を測定すると、光学距離が不十分であることがわかります(底部) |
|
Fig. 10: ICM 工程-フリンジパターンはより均一になります(上部)。光弾性応力を測定すると、光学特性が飛躍的に改良されたことがわかります(底部). |
Moldex3D シミュレーション解析を使って、PPL はICM 工程をよく理解し、潜在的に問題がある部分を検証しました。成形条件で重要なもの(例えば、射出/圧縮切り替え点、圧縮力、圧縮速度、応力分布など)を注意深く検証し、最適化することができました。
結論
PPL はMoldex3DのICM モジュールによる解析を使って、射出圧縮成形時のキャビティ内のプラスチック流動挙動を理解することができました。ICMモジュールの正確なシミュレーションはヘッドライトレンズの製造のソリューションを提供しただけでなく、成形条件の効果的な最適化を実現しました。このことが製品品質を飛躍的に改良し、厳しい製品要求に答えることができました。