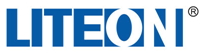
- 顧客名: Lite-On Technology Corporation
- 地域: 台湾
- 産業分野: 電子機器
- 導入製品: Moldex3D Advanced
Moldex3D導入のきっかけ
ベアリングブッシュはベアリング製品にとって重要な部品です。摩損を回避し、機械寿命を延ばすのに役立ちます。 プラスチック射出成型工程でベアリングブッシュを成形する場合、その真円度やサイズを製品仕様に合致するように製造することは簡単ではありません。よって成形工程をモニタリングし、厳格な制御を行う必要があります。もし機械の稼働中に部品サイズが規格外になれば、雑音を発生する不良品になります。このような不良品が発生すれば、製品の生産率が著しく悪化します。 製品を規格に合うように製造するには、プラスチックの充填時の流動のバランスを良くし、製品厚みを適切にしなければなりません。Lite-On Technology はMoldex3D シミュレーション解析を活用することにより、製品厚みを適切にし、ゲート位置を最適化し、製品品質を向上することにより、不良品率を飛躍的に削減することができました。
課題
- 製品の真円度の精度が低い: ベアリング回転時の振動と雑音の原因になる
- 製品の真円度に関する要求仕様が厳格: 真円度は0.05 mm に制御される必要がある
ソリューション
設計最適化と成形条件の最適化のため、同社はMoldex3D シミュレーションソリューションを導入しました。また、生産効率を向上するため、以下の項目に注目しました:
1. 改良前の設計でホットスポットが発生する部分を検出する
2. ゲート位置を変更し、メルトバランスを改良し、保圧効果を向上させる
3. バランスの悪いメルトと貧弱な保圧効果による変形を最小限に収める
4. 元の設計と改良後の設計を比較し、最良の設計を選択する
5. 円筒部に異なるノードを配置し、Z-軸方向の真円度変化を測定する
ケーススタディ
元の設計では、製品各部分における厚み変化が成形問題を引き起こす原因と考えられました。元の設計のゲート位置は、肉厚の薄い領域(1mm)にありました。しかしプラスチックメルトは予想以上に固化するのが早く、充填時に低温の金型壁に最初に接触する時点で固化が始まっていました。これにより、次の保圧段階で保圧効果が貧弱になりました。その他の問題として、肉厚の厚い領域(2.2mm)を通るフローパスの端点に、この製品の円筒形状があることです。この部分の製品厚みにより、この領域に容易に熱が蓄熱され、冷却が難しいという課題がありました。よって製品が冷却され室温まで到達すると、この部分(円筒形状)では体積収縮や反り変形が発生し、製品変形が発生してしまいました。しかしこの円筒部分の真円度の精度は、製品品質を左右するほど重要でした。従って、この部分の真円度を0.05mm以下に制御することが設計変更/最適化の主要な目標となりました。
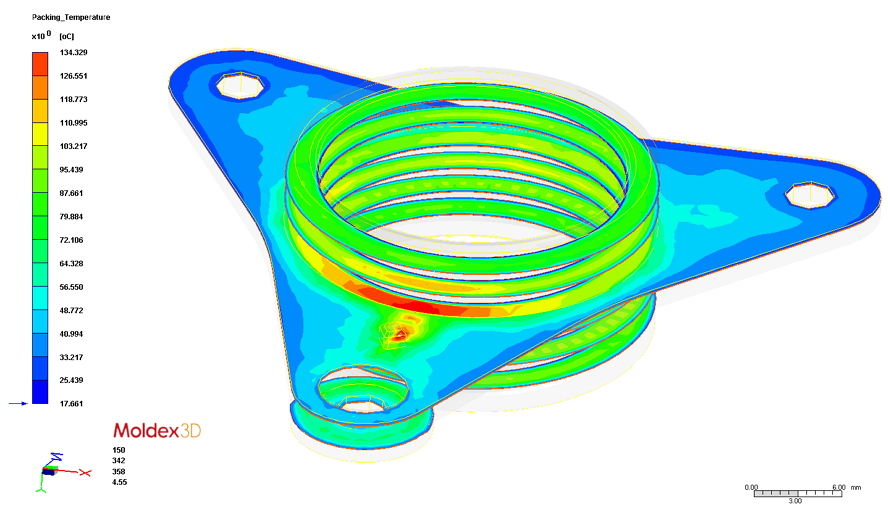
製品の肉厚変化
中心の円筒部分の収縮問題を解決し、さらに製品変更の考察を行うために2つのアプローチが行われました:
1. ゲート位置はそのままにし、中心の円筒部分の厚みを減らすことにより、変形を最小限にする
2. ゲート位置を円筒形状の円周に変更し、この部分の保圧効果を向上する
上述のアプローチ方法を元に、5つの設計変更オプションをシミュレーションし、検証しました。
Design 2: ゲートの位置は元のゲート位置のまま。円筒形状を通過するプラスチックメルトの量を減らし、体積収縮をより均一にする。円筒部分の真円度がより安定する。
Design 4: ゲート位置を円筒の円周に配置する。円筒部分の保圧に十分な圧力を維持できるが、この部分の厚みは減らないため、全体的な収縮量は依然として大きい。
Design 6: コア側から円周部分へ材料が削減され、ゲート位置をキャビティ側に移動する。しかし、円筒部分の不均一な収縮問題は依然として発生している。
元の設計と最適化後の設計でトータル変位を比較すると、 Design 2 が最も良い結果となりました。
Original Design | Design 2 | Design 3 |
![]() |
![]() |
![]() |
3ゲート | 3ゲート;材料を減らす | 3ゲートをタブに配置; 円周はそのまま |
Design 4 | Design 5 | Design 6 |
![]() |
![]() |
![]() |
3ゲートを円周上に配置 | ゲート設計はそのまま;円周近くの材料を減らす | 3ゲートを円周部分に配置;材料を減らす |
元の設計と最適化した設計の比較
元の設計と最適化後の背系のトータル変位の比較
Design 2を元に製品設計を修正し、再度測定しました。真円度が0.05mm以下になり、要求される設計仕様に合致します。
座標測定機を使って真円度を測定
メリット
Moldex3Dを導入する前、 Lite-on Technologyはブッシュベアリング部品の大量生産は難しいと考えていました。なぜなら不良品率を減らすことは簡単ではないからです。しかし同社は Moldex3D シミュレーション解析結果と実際の成形結果を検証することで、不良品率を約1%まで減らすことに成功しました。これにより、試作コストを削減し、納期短縮を実現しました。
Moldex3D の完全 3D可視化機能により、目に見えない製造上の欠陥問題を可視化できます。バーチャルに試作品製造を行い、工程最適化を行うことで、製品設計者は開発段階で簡単に設計変更を行うことができます。つまりMoldex3D は製品製造のソリューションをお客様に提供するだけでなく、競争力のある製品を実現できる能力も提供しているのです。