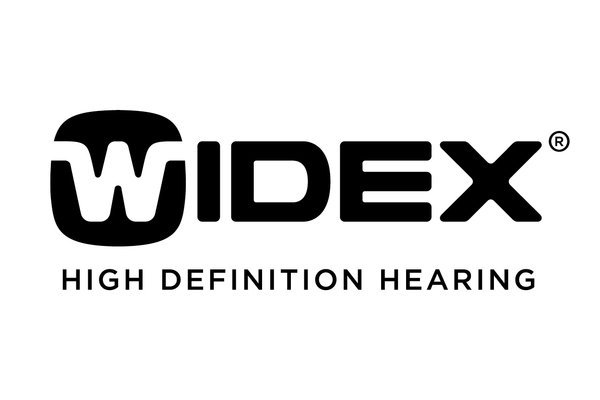
- 顧客名: WIDEX
- 業種: Medical
- ソリューション: Moldex3D eDesign
- 国: Denmark
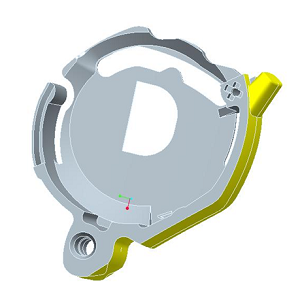
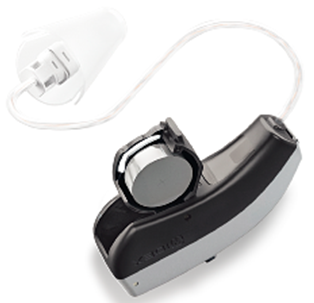
Fig.1 バッテリーホルダーのCADモデル
概要
一般的に、補聴器は非常に小さくかつ繊細な機器であるといえます。今回取り上げる事例では、Widex社は様々なゲート位置と各部品のパート板厚設計の検討にMoldex3D eDesignを利用しました。 Moldex3Dは、充填フェーズにおける流動挙動の調査、ひけマークの低減や反り変形の厳密な見極めに役立ちました。 解析結果をつぶさに確認することで、Widex社は、金型の試験を行う前の最適な設計にたどり着いたのです。 ゲート位置の変更によって体積収縮の分布がより均一になったため、最終的な反り変形発生の予測精度も向上しました。
課題
- 複雑な形状と金型
- 許容誤差の維持
- 製品表面の滑らかさ
- 流動性の高い材料
- 微小で散らばりやすい部品
- 複数の部品(ポリマーや金属)による金型製造の難化
ソリューション
Moldex3D eDesignは、容易かつ迅速にメッシュを生成します。これにより、短期間で複数の設計とその評価が可能です。True 3Dによるウェルドラインや体積収縮、または反り変形などの解析結果から、Widex社は、製品に生じる潜在的な問題を正確かつ効果的に予測できました。
メリット
Moldex3D eDesignによるゲート位置の最適化がWidex社にもたらしたメリット:
- 開発期間の短縮とコストの削減
- 金型試作期間および市場投入までに要する時間の短縮
- 製品品質の向上:反り変形の最小化、ひけと応力の除去
- 工程の許容範囲拡大または加工困難な材料の利用
- サイクルタイムの短縮と材料の節減(2次的効果)
今回の事例では、ひとつの補聴器製品に複数の部品設計(バッテリーホルダー、バッテリーコネクター、上蓋)が含まれていました。
バッテリーホルダーは薄い曲面をもつ複数の部品から成っており、Fig.1に示す黄色い部分は利用時に露出しています。このような部品ではウェルドラインの位置やひけマークがしばしば問題となるため、Widex社はMoldex3D edesignを使って部品のゲートとランナーを作成し、3D解析を行って体積収縮の問題を予測しました。
Fig.2 ゲート位置の異なる3つの設計案と、関連するウェルドライン領域(Moldex3Dの予測による)
Fig.2は、ゲート位置が異なる3つの設計案です。 Gate Location 1)元のゲート設計、Gate Location 2)第2案、Gate Location 3)元の設計と第2案を組み合わせた設計案 です。解析の結果、Gate Location 2 では重要な位置にウェルドラインが生じてしまったため、機械的な問題を避けるためにこの案は不採用になりました。
元の設計案である Gate on Location 1)はフローリーダーが必要ですが、ウェルドラインの位置は許容できるものでした。しかし、体積収縮が非常に大きくひけの問題も明らかでした(Fig.3)。 第2ゲートの追加によって、ウェルドラインの位置を保ったままで最大体積収縮を許容範囲まで低減することに成功しました(Fig.4)。
![]() |
![]() |
Fig.3 Gate Location 1 の解析結果 |
Fig.4 Gate Location 3 の解析結果 |
バッテリーコネクターには、金属インサートが中央に配置されないという問題がありました(Fig 6)。ゲート付近にバリが確認されたことから(Fig.5)、充填時にフローバランスが崩れた場合には金属インサートが移動していることがわかります。Moldex3Dの解析では、充填圧力が高く、またキャビティに流入する材料が金属の下側を流れているために金属を押し上げていることが判明しました(Fig.6)。
![]() |
![]() |
Fig.5 ゲート部分付近のバリ |
Fig.6 Moldex3Dの解析でゲート部分付近に見られた
|
上蓋に関する主な問題は、ひけや反り変形の問題につながる収縮をどのように制御するかという点でした。Widex社が行った複数の変更案のMoldex3Dによるテストの結果(Fig.7)、ひけの問題が無事に解決し、(Fig.8)反り変形の傾向も正確に予測できました。