射出成形製品の開発および生産プロセスにおいて、CAE(Computer-Aided Engineering)解析は設計エンジニアにとって不可欠な役割を果たします。CAE解析により、実際の生産前に潜在的な問題を事前に排除し、設計を最適化することが可能です。さらに、CAE解析による仮想成形トライは、適切な成形条件を見つけ出し、その後の成形トライの基準を提供します。しかし、金型開発が完了し量産段階に移行する際、製造現場ではCAE解析で得られた成形条件を直接利用することが難しく、経験に基づく条件調整に頼ることが多いです。特に新製品や新素材の場合、限られた経験しかないため成形トライプロセスが長引き、生産が遅れる可能性があります。
Moldex3DのCAE解析結果は、製品、材料特性、成形機の特性に基づいて生成されるため、解析で最適化された成形条件は実際の生産を再現します。この科学的成形は、従来の方法と比較して、成形トライプロセスを加速させ、コストを削減します。では、CAEと生産現場のデータを効果的に共有し、生産側が解析結果を成形トライの参考として簡単に取得できるようにするにはどうすればよいでしょうか。また、設計側が試作用結果を次回の製品設計や最適化の参考として簡単に参照できるようにするにはどうすればよいでしょうか。この課題は、設計と製造の間における重要なテーマとなっています。
近年、設計と製造の統合の重要性が高まっており、さまざまな展示会でその傾向が紹介されています。Moldex3Dは、生産プロセスにスムーズに連携させるため、世界的な射出成形機メーカーであるFANUC、SUMITOMO、ENGELとCAEと射出成形機の統合を実現しました。これにより、樹脂流動解析結果を迅速かつ便利に製造現場に伝達でき、成形エンジニアはこれらの条件を参考に成形トライプロセスを迅速に開始し、最適な生産条件を見つけ出すことができます。これにより、試作時間を短縮し、新素材や新製品の課題にも効果的に対応可能です。双方向のデータ交換がスムーズになると、試作用データが簡単に保存され、重要なデータがシステムに蓄積されます。これは、後の製品開発や製造における貴重な参考情報となります。設計と生産の統合が実現することで、両段階のワークフローと情報がスムーズに接続され、スマートな射出成形生産プロセスが促進されます。
Moldex3DとFANUC ROBOSHOT射出成形機の統合
Moldex3DとFANUCは、Moldex3D iSLMとFANUC ROBOSHOT LINKi2を通じてデータ交換を行います。iSLMとLINKi2は、顧客のプライベートクラウドで動作し、重要なデータの安全性と機密性を確保します。設計エンジニアはローカルでMoldex3D解析を完了後、解析結果をiSLMにアップロードします。成形トライ現場の成形エンジニアは、ROBOSHOT LINKi2を通じて成形機コントローラ上でiSLM統合解析結果を開き、追加の設備なしで成形機から直接CAE解析結果を確認し、双方向のデータ交換を行えます(図1参照)。
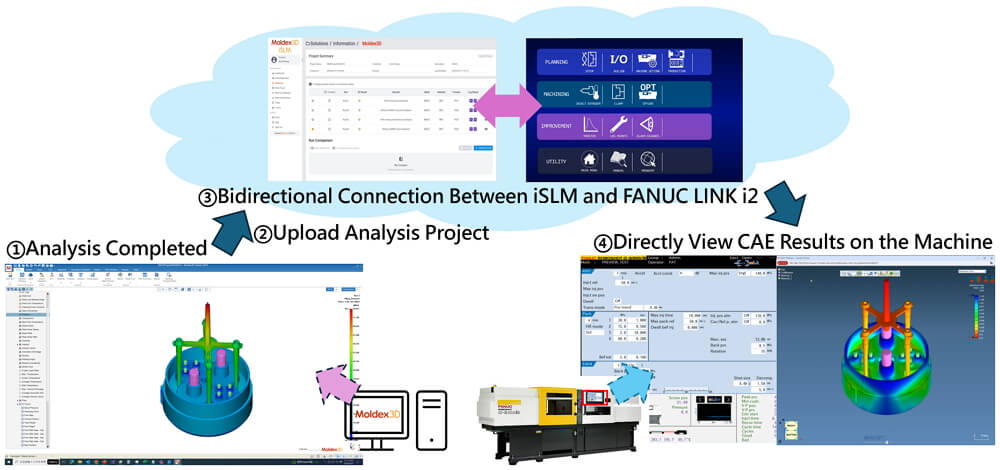
図1 Moldex3DとFANUC ROBOSHOT射出成形機の統合プロセス
成形エンジニアはコントローラ上でiSLMを開き、成形トライを行う解析結果を閲覧できます。例えば、フローフロント結果や射出圧力曲線などの解析結果がコントローラ上で直接確認可能です。成形トライを開始する際、成形エンジニアはワンクリックでCAE側の成形条件を生産側に転送し、初回の試作用条件として使用できます(図2参照)。成形エンジニアは、実際の製品品質に基づいて成形条件を微調整するだけで、量産可能な製品を得られます。成形トライ完了後、ワンクリックで微調整後のパラメータを生産側からCAE側に転送し、重要な試作用結果と経験をiSLMに保存できます。これにより、類似製品を扱う成形エンジニアや設計エンジニアが参考にでき、研究開発と生産のスピードを加速します。
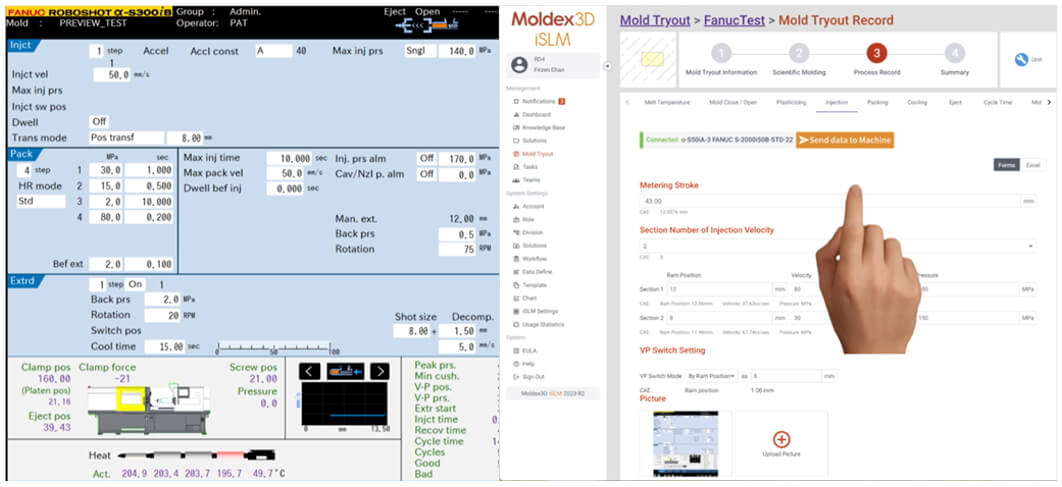
図2 ワンクリックでCAE側から生産側へ成形条件を転送
Moldex3DとSUMITOMO射出成形機の統合
Moldex3DとSUMITOMOは、SUMITOMO射出成形機が読み取れる成形条件ファイルを通じて統合を実現します。操作プロセスは図3に示されます。対応するコントローラは住友NC-10コントローラです。成形トライ前に、成形エンジニアは成形トライを行う成形機コントローラ内で金型開閉などの設定を完了し、成形条件ファイルを出力します。Moldex3D内で出力する成形条件の解析グループを開き、成形ウィザードでNC-10コントローラの実機ページを開いて成形機ファイルを入力します。ユーザーは出力する成形条件ファイルと保存場所を選択するだけで、成形ウィザードがCAE内の成形条件を成形機ファイルに自動的に書き込みます。その後、成形エンジニアはこのファイルを成形機に入力するだけで、CAE条件がコントローラに反映されます。
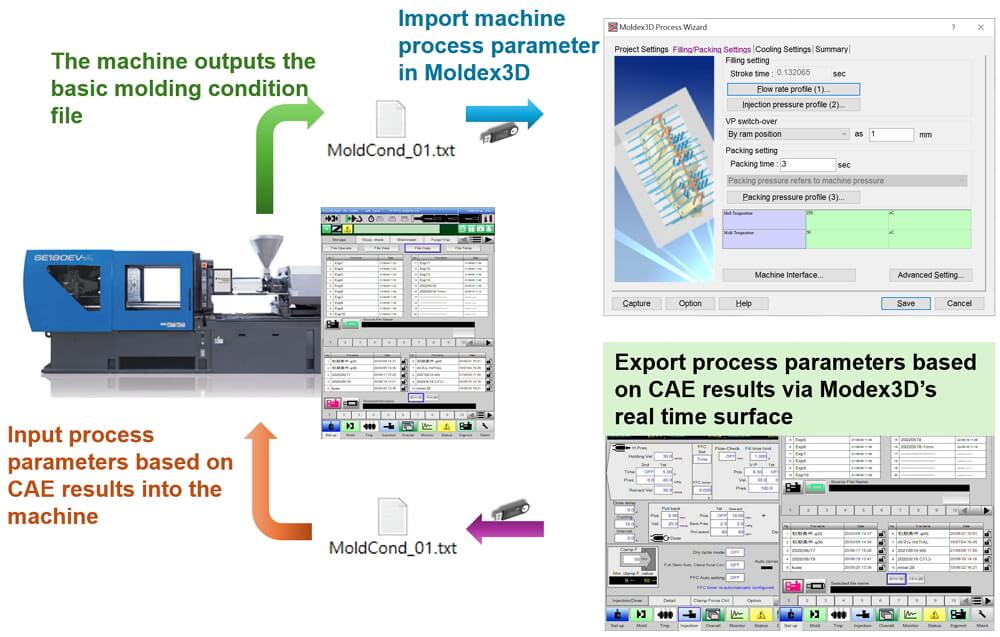
図3 Moldex3DとSUMITOMO NC-10コントローラの統合プロセス
Moldex3DとENGEL射出成形機の統合
Moldex3DとENGELの統合は、ENGELが開発した生産監視およびデータ分析システム「sim link」を通じて行われます。sim linkは樹脂流動解析ソフトウェアと射出成形機間のデータ交換プラットフォームとして機能し、シミュレーションと実際の生産を結びつけ、現在Moldex3Dの解析結果をサポートしています。操作プロセスは図4に示されます。ユーザーはローカルでMoldex3Dとsim linkの交換ファイル生成プログラムをインストールし、このインターフェースを通じて解析結果プロジェクトを選択し、双方に対応する交換ファイルを生成します。このファイルをsim linkのクラウドサービスに入力し、生産に使用する成形機を選択すると、sim linkは選択した成形機に基づいて成形条件を修正し、新しい交換ファイルを生成します。ユーザーはこのファイルをMoldex3Dに入力すると、システムが自動的に新しい解析グループを生成し、sim linkで修正された成形条件に基づく解析用成形条件ファイルを作成します。再度解析を行うと、sim linkで修正された条件に基づく新しい解析結果が得られます。このプロセスを繰り返し、結果が実行可能であると確認された場合、ユーザーはsim linkのクラウドサービスを通じて成形機が読み取れる成形ファイルを生成し、成形エンジニアはこのファイルを射出成形機に入力するだけで成形トライを迅速に開始できます。
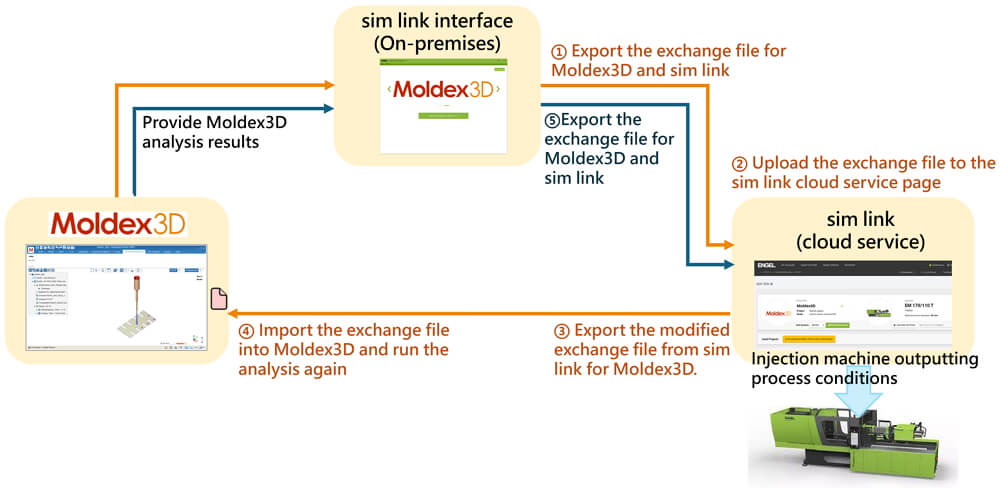
図4 Moldex3DとENGEL射出成形機の統合プロセス
結論
設計と製造の統合により、樹脂流動解析結果を製造現場に簡単に伝達でき、成形エンジニアが成形トライ時の参考成形条件として活用することで、成形トライプロセスを加速します。また、この統合により、重要な試作用データがシステムに保存され、将来の設計開発や生産の貴重な基礎となります。Moldex3Dは射出成形機との統合を通じて、さまざまな製品の成形トライの課題に共に立ち向かい、インテリジェントな射出成形の未来を共に創造します。