技術サポートチーム エンジニア 鄧詠心
- 顧客名:台湾大学
- 産業:教育
- 導入ソリューション:射出圧縮成形(ICM)、流動解析モジュールFlow、保圧解析モジュールPack、そり変形解析モジュールWarp、光学解析モジュールOptics
台湾大学(NTU)の前身は、日本統治時代の1928年に創立された台北帝国大学です。1945年11月15日、台北帝国大学は正式に台湾大学に改名され、初代校長には羅宗洛博士が着任しました。現在、台湾大学には11学部、54学科、108の大学院研究科、50以上の国家・学術レベルの研究センターがあります。学生総数は専門職学部の学生を含めて32,000人を超えており、そのうち学部生が17,000人以上、大学院生が15,000人以上となっています。大学院生の人数が学部生とほぼ同数にのぼり、NTUは研究型大学として成功を収めています。
概要
従来の複数セットのレンズによる厚みの問題を解決するために、薄型、多機能、配列の特性を備えたマイクロレンズを開発します。以前の扇形ゲートでのマイクロレンズアレイの製造とは異なり、本事例では、高速で均一、かつ良好な光学特性を備えたマイクロレンズアレイ成形プロセスを展開しています。成形解析ソフトMoldex3Dを活用して様々なランナーシステムの長所と短所を調査し、従来のランナーシステムにおけるコールドランナーの樹脂のロスを改善し、基板成形の実現可能性を検証し、シミュレーション結果を解析して製品設計を最適化しました。最終的に、実際の成形実験において、4インチ基板上に高品質の両面マイクロレンズアレイを製作することに成功しました。
課題
- ランナーの設計を改善し、材料を節約しつつ単一金型の半完成品数を増やす。
- Moldex3Dを活用してプロセスの実現可能性を検証し、金型試作の繰り返しにかかる時間とコストを削減する。
- 製品のそり変形や光学特性を最適化し、残留応力が低く、高精度で優れた光学特性を備えたマイクロレンズアレイを製作する。
導入ソリューション
台湾大学のチームは、Moldex3Dを活用して金型設計の実現可能性を分析し、金型試作を繰り返すためにかかる修正時間やコストの削減に貢献しました。また、成形状態、残留応力、そり変形の程度から、そりや光学特性に大きな影響を与える指標因子を特定し、タグチメソッドを用いて最適なパラメータを求めました。更に、インモールド成形の角度から射出成形(IM)と射出圧縮成形(ICM)の違いを解釈し、4インチ基板上に両面マイクロレンズアレイを製作することに成功しました。
成果
- 従来の扇形ゲートの代わりにダイレクトゲートを使用することで、材料使用率が18.8%から66.3%に大幅増加
- 射出圧縮成形後の収縮率は1.5~2%まで下降し、タグチメソッドによる最適化で更に1.5%未満に下降
- Moldex3DによりIMとICMの差異、長所・短所の検証に成功
- 製品の複屈折差を改善して、光学性能が向上
ケーススタディ
現今のバーチャルリアリティとウェアラブルデバイスは急速に発展しています。従来のレンズは複数のレンズで構成されており、厚すぎるという問題が発生しやすいため、薄型・多機能・配列化されたマイクロレンズの開発が不可欠です。扇形ゲートで製造されるマイクロレンズアレイ(図1)とは異なり、本事例ではダイレクトゲートを使用して、高速で均一、かつ良好な光学特性を備えたマイクロレンズアレイ成形プロセスを展開しました。
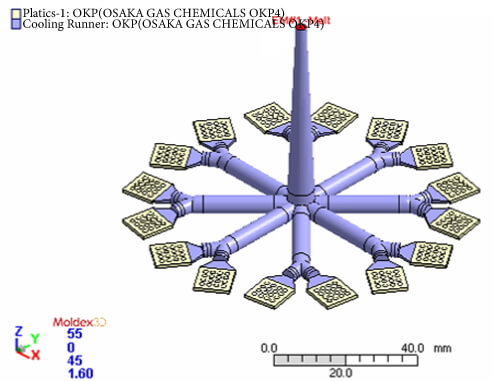
図1 元のランナー設計
ダイレクトゲートを使用して一度に48のマイクロレンズアレイを製造することで(図 2)、生産効率が大幅に向上し、材料の無駄を削減 (表 1)できました。
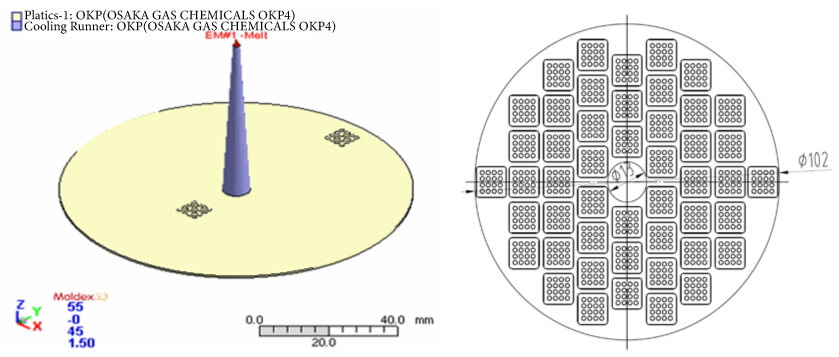
図2 ダイレクトゲートと最終完成品の概略図
表1 コールドランナーの扇形ゲートとダイレクトゲートの比較
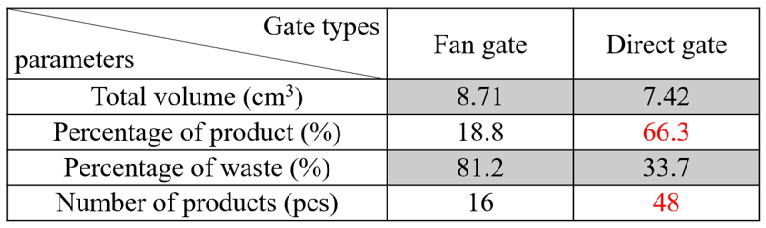
台湾大学のチームは、タグチメソッドを用いて残留応力とそり変形を軽減するための射出成形 (IM) と射出圧縮成形 (ICM) の最適なパラメーターを求めました。溶融温度、射出速度、保圧圧力、冷却時間などの射出成形における相対的に重要な要素とは異なり、射出圧縮成形では、溶融時間、圧縮ギャップ、圧縮時間、圧縮成分が保圧圧力と光学特性に顕著な影響を与えます。図3と図4は、IMとICMのそり変形およびフリンジ(縞)パターンの比較です。結果は、ICMで総変位と収縮が低減され、IMよりも良好な光学特性を備えていることを示しています。
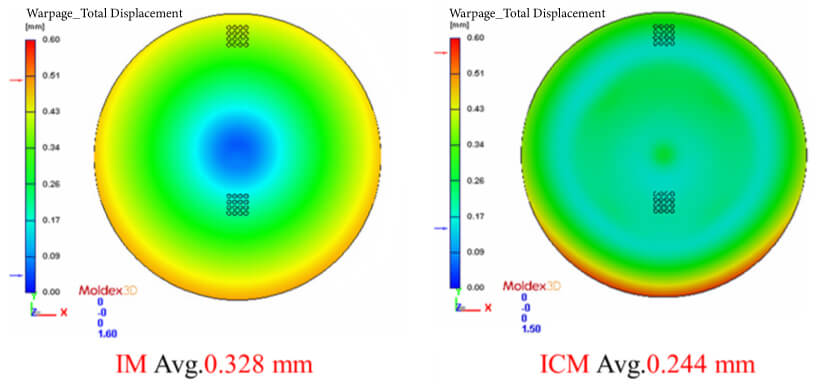
図3 IMとICMの総変位量の比較
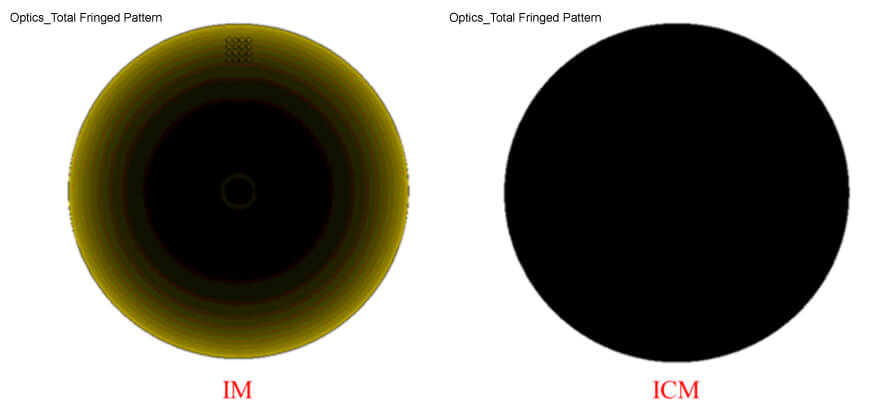
図4 IMとICMのフリンジ(縞)パターンの比較
最終的に、シミュレーション結果は実際の成形実験により検証され、同様のフリンジパターンと光学特性を備えた両面マイクロレンズアレイを4インチ基板上に製作することに成功しました(図5)。OKP4を材料とした場合、ゲート付近の射出成形領域のみにフリンジ(縞)パターンが観察され、射出圧縮成形においてこの現象は観察されませんでした。図6に示すように、成形されたマイクロレンズアレイは集束機能と鮮明な結像を示しました。Moldex3Dシミュレーション解析ソフトのサポートにより、両面マイクロレンズアレイ成形技術と効率は大幅に向上し、また現今の光学業界の高性能・小型・軽量のニーズを満たすことができました。
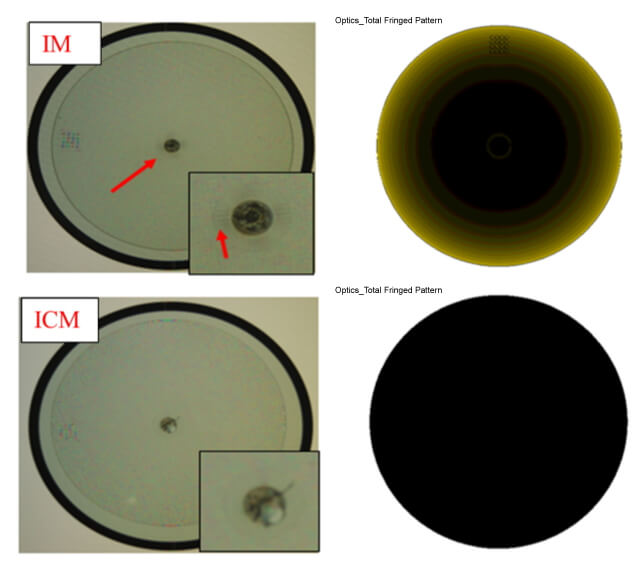
図5 シミュレーションされたフリンジ(縞)パターンと実際に成形されたフリンジ(縞)パターン
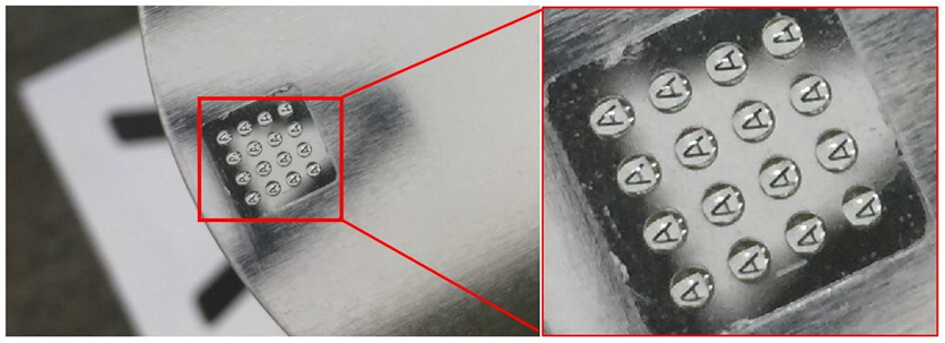
図6 成形されたマイクロレンズを通して見た画像
結論
本事例では、Moldex3Dを活用して様々なランナーの設計と成形パラメータの長所・短所を解析しました。元の扇形ゲートの設計をダイレクトゲートに置き換えることで、材料利用率が66.3%に向上し、マイクロレンズアレイの製造に成功し、材料使用率は扇形ゲートの3倍に達しました。射出成形および射出圧縮成形パラメータを最適化した後、そり変形および収縮の程度も大幅に改善されました。最終的に、実際の成形実験において両面レンズアレイの製造が完了し、結果、Moldex3Dシミュレーションとの高い一致を示しました。