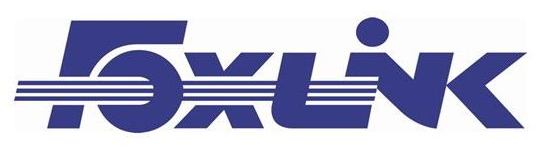
- 顧客名: Foxlink Image Technology Co., Ltd.
- 地域 : 台湾
- 業種:Electronics
- 導入ソリューション:Moldex3D Advanced; Flow, Pack, Cool, Warp, Designer BLM, Fiber
概要
事例1では、グリッド構造に微細な特徴をもつスキャナカバーを取り上げます(Fig. 1)。射出成形における課題のひとつとして、細かな形状部によるショートショットやウェルドラインの問題があります。設計変更と金型試作のコストを抑えるためには、設計の初期段階で製品の成形性を検証しなければなりません。事例2では、スキャナのギアを取り上げます。動作を安定させるために寸法精度に対する要求がほかの組立品より高く、また、組立のしやすさを確保するために表面(ゲートエリアなど)を滑らかにする必要があります。Moldex3Dの利用により、さまざまな成形不良を事前に評価し、また成形品質の最適化を図ることができます。
Fig. 1 スキャナカバー:細かいグリッド構造があり、射出成形が困難な形状
課題
- 複数のゲート設計を検討し、スキャナカバーのショートショットを評価する
- スキャナギアと金型設計の最適化により寸法精度を満足する
導入ソリューション
Moldex3D充填解析を用いて、ショートショットの欠陥と流動バランスを評価します。さらに、保圧解析・冷却解析を用いて体積収縮とオーバーパックの影響を評価します。
メリット
- オリジナル設計において発生するショートショットの予測
- 寸法精度低下の原因特定。また、成形収縮と蓄熱の問題を改善
ケーススタディ
まず、スキャナカバー(事例1)において、グリッド構造内の細かい形状によって生じるショートショットの問題が、ゲート設計の変更で改善可能であるかを確認する必要がありました。さらに、スキャナギア(事例2)の成形品の最終寸法を予測し、製品品質低下の主要因を特定することで製品規格に適合する設計を見つける必要がありました。
最初に、Moldex3Dで、スキャナカバーのゲート位置案を2つ、グリッド構造または中心部を含めて解析します(Fig. 2)。充填結果から、どちらの設計案も、同様のショートショットのリスクがあることが分かりました。そこでFoxlinkは、部品を別々に成形することにしました(Fig. 3)。
Fig. 2 2種類のゲート設計におけるショートショット(Moldex3D充填解析の結果より)
Fig. 3 ゲート設計の変更によりショートショットは改善せず。部品を2つに分けて成形することを決定
スキャナギア(事例2)において、スキャナギアの流動がアンバランスであり、また、保圧が高いことがMoldex3D成形解析によって示されました。この2つが原因となって、寸法精度に影響する成形品の変形が生じていました(Fig. 4)。そこで、Foxlinkは成形品の変形を改善するため、3つの設計変更案を提案しました。
Fig. 4 スキャナギアの上部と底部(Ø X と Ø Y)の差を規定値内に収める
Fig. 5 スキャナギアのパート変形改善を目的とした3つの設計変更案
FoxlinkはMoldex3D充填/保圧/冷却解析を用いて、オリジナル設計と、3つの設計変更案を検証しました。その結果、スキャナギアの成形品における流動のアンバランスとオーバーパックの問題解決には、ゲート位置の変更、パーティング面の移動、成形品設計(局所板厚)の変更が必要であることがわかりました。最終的に、Fig. 5にType Cとして示す設計変更案では、充填圧力と蓄熱の改善、成形品収縮の不均一等の改善が見込めることがわかりました。結果的に変更案を盛り込んだ実際の金型で、型開き後の上部と底部(Ø X と Ø Y)の差は0.03mm前後に収まりました。この数値は製品の規格内であり、Moldex3Dの予測と一致するものです(Fig. 6)。
Fig. 6 オリジナル設計と、設計変更案を対象とした、保圧・変形解析結果
結論
Moldex3Dを利用することで、Foxlinkは、ショートショット・エアトラップ・ヒケマーク・反り変形などの成形不良を、低コストかつ迅速に予測することができました。さらにMoldex3Dを活用することで、実際の生産開始前に、生産コストの削減とリスク回避が可能になりました。