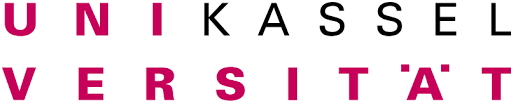
- 顧客名:University of Kassel
- 国名:ドイツ
- 業種:教育/学術
- 導入ソリューション:Moldex3D Advanced Package、Foam Injection Molding Module
概要
このプロジェクトでは、主に射出発泡成形プロセスにおけるコアバック技術について検討しました。倍率を引き上げることで低密度パーツの生成を可能にし、さらに射出発泡成形における気泡の均一化を図りました。標準的なコアバックプロセスと比較すると、本事例の製品は、部分的な膨張により気泡形成が一部に限定されています。膨張エリア・非膨張エリアのどちらにおいても、気泡構造の形成は境界条件とプロセスパラメータ設定の影響を受け、さらに相互作用により非常に複雑なものになっています。Moldex3D射出発泡成形モジュールの利用により、構造形成のプロセスの理解とそれに基づくプロセスパラメータ調整が可能となります。
課題
- 材料、プロセス設定、幾何学的境界条件など、コアバック結果に影響する各要素間の相互作用
- 発泡プロセスの実際の様子は確認不可能
導入ソリューション
Moldex3Dを用いて、1)射出発泡成形におけるコアバックの様子を解析、2)キャビティ内の発泡挙動を予測、3)適切なプロセスパラメータに調整します。これにより、理想的なコアバック結果を得ることができます。
メリット
- 射出発泡成形における部分的なコアバック技術の理解
- 気泡形成プロセスの可視化
- 定性実験結果の解析による検証
ケーススタディ
カッセル大学はMoldex3Dを利用して、射出発泡における構造形成のプロセス全体を詳細に解析しました。Moldex3Dは、コアバックプロセスの境界条件設定をサポートしており、充填・保圧プロセス中の各時点における気泡サイズ、気泡密度、製品密度を予測することができます。また、Moldex3Dのセンサーノードは、膨張・非膨張エリアにおける圧力と気泡サイズとの関係の理解にも非常に役立ちます。
充填段階で形成される気泡は、体積膨張による2次発泡の発生前に、保圧圧力の影響を受けて消失します。Fig. 1に本事例における気泡サイズの予測を示します。ここから、コアバック完了後に気泡が大きく膨張していることが確認できます。Fig. 2に示す解析結果は、気泡が大きいほど気泡密度が低くなることを示しています。
Fig. 1 気泡サイズ。上:充填・保圧段階(体積膨張前)、下:充填完了後(体積膨張後)
Fig. 2 気泡密度。上:充填、保圧段階(体積膨張前)、下:充填完了後(体積膨張後)
Fig. 3に製品密度の変化を示します。膨張エリアにおける気泡形成によりそのエリアの製品密度は大幅に低下していますが、非膨張エリアの製品密度は未発泡材料の密度と同等です。
Fig. 3 製品密度。上:充填、保圧段階(体積膨張前)、下:充填完了後(体積膨張後)
Moldex3Dは、キャビティ内の発泡挙動の確認が可能な「センサーノード」機能を備えています(Fig. 4)。非常に実用的なこの機能を使って、キャビティ内の気泡形成を詳細に理解することができます(Fig. 4)。
Fig. 4 膨張エリアA(SN5)と非膨張エリアB(SN7)における、センサーノード上の圧力と気泡サイズのXY曲線
解析により、射出発泡成形におけるコアバック技術の効果を詳しく知ることができます。SCF含有量(発泡剤含有量)、膨張率(コアバック距離)、遅延時間、保圧圧力と保圧時間などのパラメータの変化を理解することができました。
Fig. 5はプロセス設定を変更した場合の解析結果です。SCF含有量(発泡剤含有量)と実際の製品構造との関係を示しており、解析結果と実験結果は、ともに、SCF含有量が多いほど気泡は小さくなることを表しています。実験データからもMoldex3Dの予測精度の高さが証明されています。
Fig. 5 SCF含有量と気泡サイズの関係
結論
カッセル大学は、Moldex3Dを利用することで、気泡形成プロセスを可視化して射出発泡成形における部分的コアバック技術への理解をさらに深めることができました。また、Moldex3Dを用いた解析による定性実験検証に成功しました。