- 顧客:AKSEM Plastik Metal Kalip San. ve Tic. Ltd.Sti.
- 業種:自動車
- ソリューション: Moldex3D eDesign
- 国: トルコ
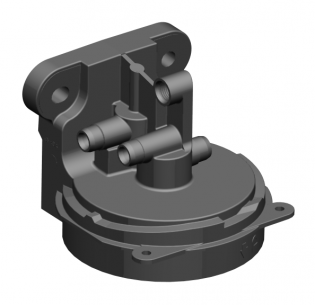
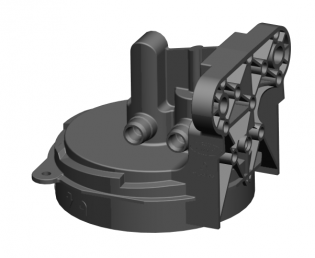
これは自動車部品(オイルフィルターヘッド)です。この製品の安全要求仕様により、
製品の変形公差および寸法偏差は非常に小さいのが特徴です。
概要
自動車部品(オイルフィルターヘッド)のケースでは、製品の安全要求仕様により、製品の変形公差および寸法偏差は非常に小さいのが特徴です。自動車業界では部品の軽量化や製造コストの削減という観点から、プラスチック射出成形(PIM)で製造された部品が広く使用されてきました。 収縮率は成形工程にとって重要な変数です。しかし収縮率を許容範囲内に維持することが非常に難しい場合があります。特に円筒形状の部品のように、公差や寸法偏差が小さい部品の場合です。このような場合に金型充填シミュレーション解析を行うことにより、収縮に問題がある部分を見つけ、収縮率を適切な範囲内に維持することが可能です。またMoldex3D 解析を利用することにより、実際の金型設計、製造に必要な情報を得ることができます。従来のようなトライアンドエラーの手法を用いるよりも、シミュレーション解析を行うことで時間とコストを削減できます。このシミュレーション解析は非常に経済的なアプローチだと言えます。さらにMoldex3D DOE(実験計画法)モジュールを使用すれば、成形工程における重大な成形条件パラメータを特定し、成形条件を最適化するための値を算出できます。
課題
この部品のケースでは、円筒部にできる丸い変形、サーフェイスの平坦度、コールドウェルドラインが最も深刻な問題でした。このような不均一な収縮はオイル漏れの潜在的な要因になるため、円筒部の丸い変形を解決しなければなりませんでした。その他の問題も、将来的にオイル漏れの要因になることも考えられます。しかし潜在的な成形欠陥に注目し、金型キャビティ内部の挙動を可視化することは、簡単ではありません。よってこのケースでは製品品質を確実にし、金型試作の反復回数を最小限にすることを目指しました。
ソリューション
製品品質の向上のため、Moldex3D DOE (実験計画法) を用いて製造工程で最も重要なパラメータを特定しました。また実際に金型試作を行い、Moldex3D シミュレーション解析と一致することも確認しました。Moldex3D ソリューションを利用することにより、 ASKEM 社は変位の許容値を見つけ、製品のサーフェイスの平坦度を制御することに成功しました。またこれは、製造コストと時間の大幅な削減をもたらしました。
最も最適化されたパラメータを Moldex3D DOE Expertで特定します
ケーススタディ
まず最も重要な作業は、最終製品の寸法値を決めることです。この値はMoldex3D解析とDOE モジュールのシミュレーション結果から求められます。この寸法値の解析結果は潜在的な収縮問題の解決に必要であり、また収縮率や製品の寸法偏差を適切にするための金型寸法調節に必要です。つまりMoldex3D解析を行うことで、円筒部分の丸い変形を矯正し、さらに品質を向上させることができます。
そり変形_トータル変位: 0.102mm~1.53mm
金型の設計段階で、Moldex3Dのそり変形解析結果を元にスチールと製品寸法データが修正されました
次に重要な作業は、そり変形やウェルドライン問題を回避するためにエアーベントの最適な位置を決定することです。Moldex3D解析結果から、前もってエアーベントの位置として可能な場所を確認できます。このようにエアーベントの場所を調節することで、潜在的なエアートラップ問題を回避することが可能です。最良のエアーベントレイアウトを検証し、サーフェイスの平坦度を改良することができます。またコールドウェルドライン問題もうまく制御できます。
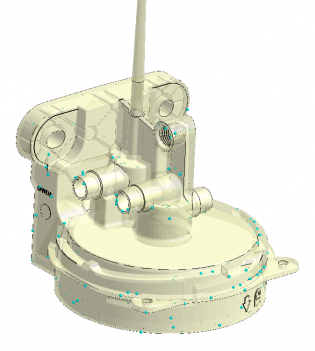
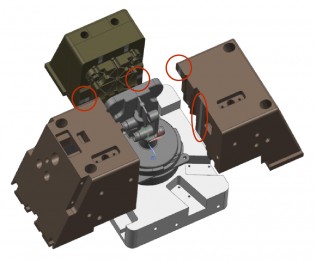
金型設計時にエアーベントレイアウト (右) を検証し、エアートラップ予測 (左) を実行
さらにこのケースではプラスチック製のオイルフィルターヘッドがボウル部分に装着されるため、この寸法精度は非常に重要です。従って実際の金型製造の前に、全ての潜在的な問題を検証しておかなければなりません。これが余分な製造コストを回避し、製造リードタイムの短縮へとつながります。
このようにMoldex3D 解析とMoldex3D DOE モジュールを利用することで、 ASKEM 社は事前に製品欠陥の発生箇所を予測するだけでなく、重要な成形条件パラメータを事前に特定し、最適化することができました。これにより納期短縮、品質向上が実現しました。
結論
Moldex3D シミュレーション解析を行うことで、金型設計に有効な情報を取得できます。 Moldex3D シミュレーション解析結果と実際の成形試作品を比較すると、 Moldex3D が提供するデータは正確かつ信頼性が高いことがわかります。ユーザーにとってさらに重要なことは、製品品質の向上と生産性が向上することで製造コストの削減が実現します。このケースでは Moldex3D はプラスチック射出成形シミュレーションを正確に検証しました。このようにMoldex3Dは製品設計と金型製造をつなぐ有益なプラットフォームを提供し、製品および金型の設計最適化と設計検証を可能にします。